Metal Spraying
Metal spraying or mettalised coatings are finding increasing importance. In this process, the heated metal particles from a metal gun are impinged against the roughened metal surface to be coated. Molten metal particles over striking the base metal surface flatten in flakes and interlock with the surface irregularities. Such sprayed coatings are continuous but somewhat porous. Metal spraying offer definite advantages over the other methods because of its greater speed of working, applicability to big surfaces and the ease of application of thick coatings even to restricted areas. Moreover, the particles of the coated metal from a work hardened surface due to impact. This results in a fairly hard coating of high wear-resistance. Though, the adhesion strength of such coatings is usually much less than that obtained by hot dipping or electroplating. Therefore it is necessary to have a clean and roughened metal surface on which a proper adhesion could be secured. Generally, the surface is roughened by sand blasting. Also sprayed coatings have a rather porous texture and tend to catch soot and other forms of contaminations.
Mettalizing is usually done by automatically feeding a metal wire at a controlled rate through the mettalizing tool or "gun" . Air, oxygen and a combustible gas are supplied to the gun by means of hoses and form a high temperature high velocity flames around the wire tip. The wire tip is constantly melted off, and the liquid metal particles are directed at the work by the high velocity flame. When they strike the surface, these particles flatten out to form irregularly shaped disks. At the same time they are forced into surface pores and irregularities to provide some mechanical interlock with previously deposited material. Cooling is very speedy and a thin oxide film forms on the exposed surfaces of the deposited particles. The nature of the oxides formed under metallizing conditions determines to a great degree, the physical properties of the deposit. Metals that compose dense, tenacious oxides having good physical properties, such like aluminium bronze, chromium steel, or silicon aluminium alloys, relatively high strength in the sprayed form. Metals that form loose, fragile oxides, such like the brasses and copper generate coatings of low strength.
The wear resistance of sprayed metals is normally very good, but metallizing is not appropriate for service involving heavy impact or extreme abrasion or where highly localised loads are applied. Metallizing is best suitable for applications involving light abrasive wear, corrosion-resistant surface to cheap base materials.
Another method of metallizing employs an oxyacetylene powder gun, as illustrated in Figure The gun might spray metal powder in place or over almost any contoured surface. This is essential to post-heat the coated surface to fuse the sprayed deposit. The powder gun might apply thin coatings and is useful for spraying hard, corrosion-resistant alloys. Most of these alloys are cobalt based or nickel based materials having chromium, carbon and silicon. Aluminium, tin and zinc powders might also be sprayed by the powder gun.
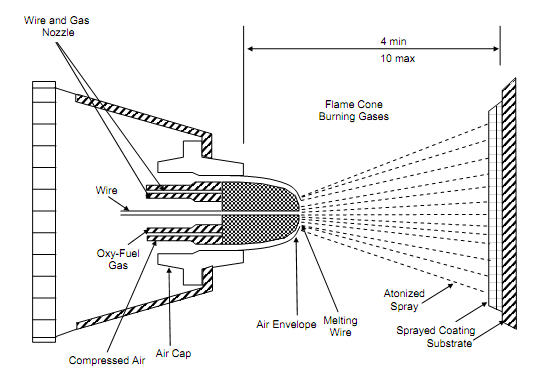
Figure: Cross-section Diagram of a Wire Gun for Metal Spraying