Modes of Automatic Control:
A mode of control is the manner in that a control system makes corrections associatively to an error which exists among the desired value (setpoint) of a controlled variable and its real value. A mode of control is used for a specific application depends on the features of the procedures being controlled. For instances, a few processes could be operated over a wide band, although others must be maintained extremely close to the setpoint. Also, a few processes modifies associatively slowly, although others change almost instantly.
Deviation is the difference among the setpoint of a procedures variable and its actual value. This is a key term used whenever discussing several modes of control.
Four modes of control generally used for most of applications are:
proportional
proportional plus reset (PI)
proportional plus rate (PD)
proportional plus reset plus rate (PID)
Every mode of control has features benefits and limitations. The modes of control are elaborates in this and the further various sections of this module.
In the proportional (throttling) mode, there is a continuous linear relation among value of the controlled variable and position of the last control element. Instead of, amount of valve movement is proportional to amount of deviation.
Below figure displays the relationship among valve position and controlled variable (temperature) features of proportional mode. Remember in which valve position changes in exact proportion to deviation. In addition, the proportional mode responds only to amount of deviation and is insensitive to rate or duration of deviation. At the 2 minute and 4 minute marks, while the temperature returns to its setpoint value, the valve returns to its initial position. Those is no valve correction without deviation.
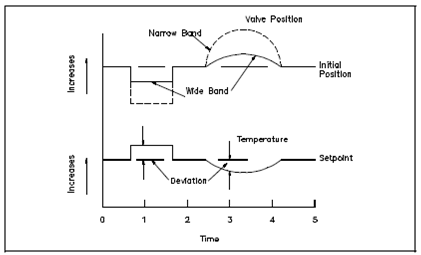
Figure: Relation between Valve Position and Controlled