Nomenclature of Milling Cutter
The nomenclature of milling cutter includes various elements and angle of cutters.
The part of the cutter to which the teeth are formed or attached at its periphery.
Edge formed by the face and the circular land or the surface which is forming the primary clearance.
The surface adjacent to the cutting edge on which the chip impinges as it is cut from the work.
Gash or flute is the chip space between the back of one tooth and the face of the next tooth.
The curved surface which joins the face of one tooth to the back of the tooth immediately ahead.
The part of the back of the tooth which is adjacent to cutting edge.
Included angle between the land and the face of tooth is called lip angle.
It is the angle between land surface (or a line passing through land) and a tangent to the periphery at the cutting edge. For the most of the cutters the clearance of 5o is provided.
- Secondary Clearance (Relief) Angle
To control the land width, a secondary clearance is ground on the tooth. It is the angle between back of teeth and a line passing through land. It is usually 3o greater than primary clearance angle.
The angle between face of the cutter and a radial line passing through the tooth of cutting edge. It facilitates removal of chips. The radial rake angle usually ranges from 10o to 20o. Larger angles are adopted for milling soft materials and smaller angles for harder material. Carbide tipped cutters are provided with a negative rake angle which varies from 10o to 15o.
The angle between the tangent to helical cutting edge and the axis of cylindrical cutter (or line parallel to axis) is called helix angle. Standard helical cutters have a helix angle of 20o to 30o.
It is the angle between the face of the tooth and axis of the cutter. It has cutting edges on periphery as well as on face. It has relief angles, clearance angle and rake angles on periphery cutting edges as well as on the face cutting edges.
Table 8 : Recommended Angle for Milling Cutters
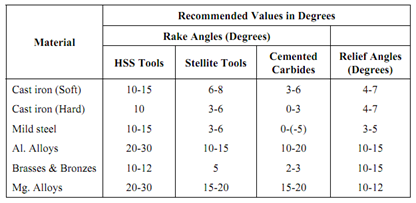