Maintenance System Optimisation
We know already that the maintenance system could be broadly divided into the following two categories:
- Breakdown maintenance (B.M.) and
- Preventive Maintenance (P.M.)
It is very clear that no machine is completely immunized to failures. According to Murphy, if a failure can occur, it will. In view of this certain amount of breakdown maintenance is necessary for any machine, even though the best preventive maintenance practices are being observed. On the other hand, the preventive maintenance is not required (or much close monitoring may not be necessary) on some machines which are not critical in the production chain (for example low cost machines, stand-by equipment etc.). The cost of the preventive maintenance will be more on such machines and it is not worthwhile. Therefore it is important to establish a maintenance system with a blend of these two maintenance practices (BM and PM) in a right proportion. Thus optimization of maintenance system can be done by classifying the machinery into certain groups based on their criticality or any other characteristics. Usually, V-E-I-N or C-I-N or V-E-D are used to classify the machinery. Once the machines are classified the amount of breakdown maintenance and the amount of preventive maintenance can be decided and planned according to their categories.
For equipment or machinery which has low criticality, such as a lathe or a milling machine in a process layout can be considered as 'not very important' (i.e. Normal category), because the breakdown on such machines will not affect the total production. Of course, it will have very minor effect as there are other stand-by machines can be used or the same operation can be done by some other machine by little adjustments or design changes of tools. In the worst case the work can be subcontracted with any local parties. So for such machines, one could go for Breakdown Maintenance even.
Now, consider a CNC machine on the same shop floor. The items finished on it are of high precision and breakdown of the CNC machine would stop the production totally. Hence this machine comes under high critical zone, and therefore, for such machinery Preventive Maintenance is worthwhile and must be planned with good amount of time. Similarly power generation system, on which running of all the machinery depend, must be under preventive maintenance system. Thus, the percentage of Breakdown and Preventive Maintenance is determined for various grades of machinery depending on their importance or criticality.
High
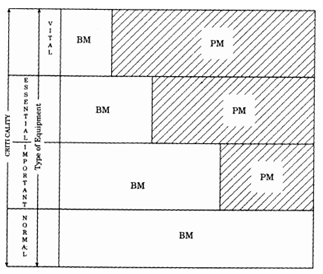
Low Type of Maintenance (Breakdown/preventive) -----→
Figure: V-E-I-N Analysis for Maintenance System Optimisation
In the Figure, the V-E-I-N Analysis for maintenance system optimization is interpreted. For vital equipment, some percent say 5-10% of Breakdown Maintenance may be planned and the rest of the time may be allocated to preventive or condition based maintenance. (5-10% of BM is due to the fact that in spite of best preventive maintenance, a system may fail).
For normal equipment, no Preventive Maintenance has been shown. There is only Breakdown maintenance. However, if required up to 10% PM may be allocated.For Important and Essential equipment, the PM and BM should be planned in right combination ranging between 30-70 percentages. The right maintenance mix can contribute to the organization in the following way.