Cost of Quality
The cost of quality is includes all costs incurred in the pursuit of quality or in performing quality related activities. Cost of quality studies is conducted to give a basics knowledge for the present. Cost of quality is to identify opportunities for reducing the cost of quality and; to give a normalized basis of comparison. The basis of normalization is almost every time dollars. Once we have normalized quality costs on a dollar basis we have the necessary data to evaluate where the opportunities lie to improve our technology. Moreover we can evaluate the effect of changes in dollar-based terms.
Quality costs may be differentiated into costs associated with appraisal, prevention, and failure. Prevention costs include:
- Test equipment
- Training
- Quality planning
- Formal technical reviews
Appraisal costs include activities to gain insight into product condition first time by each process. For examples of appraisal costs include:
- Inter process and In-process inspection
- Equipment calibration and maintenance
- Testing
The Failure costs are costs which would disappear if no defects appeared before shipping a product to the customers. The Failure costs may be subdivided into external failure costs and internal failure costs. The Internal failure costs are that costs incurred when we detect an error in our product prior to shipment. Internal failure costs are including:
- Rework
- Repair
- Failure mode analysis
The External failure costs are the costs which is associated with defects found after the product has been shipped to customer. For examples of external failure s costs are include:
- Complaint resolution
- Replacement and Product return
- Help line support
- Warranty work
By the expectation the relative costs to repair and find a defect increase dramatically as we go from prevention to detection and from internal failure to external failure. The Figure 9.1 is based on data collected describe by Boehm [BOE81], illustrates this phenomenon.
More recent anecdotal data is reported through Kaplan and his colleagues [KAP95] which is based on work at IBM's Rochester development facility:
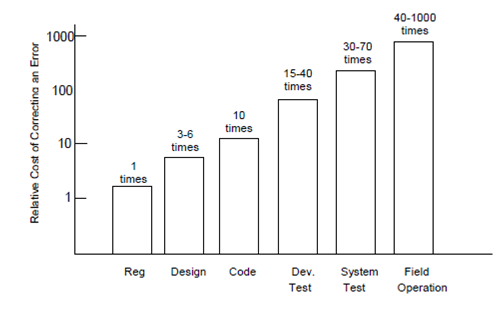
Fig - Relative cost of correcting on error
A total of 7053 hours was spent inspecting 2, 00,000 lines of code with the result which 3112 potential defects were prevented. Suppose a programmer cost of $40.00 per hour the grand cost of preventing 3112 defects was $282,120 /roughly $91.00 per defect.
By compare these numbers to the cost of defect removal once the product has been shipped to the customer. Assume that there had been no inspections but that programmer's only one defect per 1000 lines of code and had been extra careful significantly better than industry average escaped into the shipped products. That would mean that 200 defects would still have to be fixed in the area. At an estimated cost of $25.000 per area fix the cost would be $5 million or approximately 18 times more expensive than the gross cost of the defect prevention effect.
It is true that IBM produces software which is used through 10,000 of customers and that their costs for field fixes may be higher than average. This in no way negates the results noted above. Even if the average software company has field fix costs which are 25 % of IBM's the other have no idea what their costs are!, the cost savings related with assurance activities and quality control are compelling.