Non-Variable Reducing Valve:
The controlling diaphragm will transmits a downward force which tends to open the auxiliary valve. A downward force is exerted through the adjusting spring that is controlled through the adjusting screw. Decreasing pressure from the main valve outlet is bled back to a chamber beneath the diaphragm to counteract the downward force of the adjusting spring. A position of the auxiliary valve, and eventually the position of the main valve, is determined through the position of the diaphragm. A position of the diaphragm is determined through the strength of the opposing forces of the downward force of the adjusting spring versus the upward force of the outlet reduced pressure. Another reducing valve work on the similar basic principle, but might use gas, pneumatic, or hydraulic controls in place of the screw and adjusting spring.
The Non-variable reducing valves, described in Figure, exchange the adjusting spring and screw along with a pre-pressurized dome over the diaphragm. A valve stem is linked either directly or indirectly to the diaphragm. A valve spring below the diaphragm keeps the valve closed. Since in the variable valve, then reduced pressure is bled by an orifice to beneath the diaphragm to open the valve. Valve position is determined through the strength of the opposing forces of the downward force of the pre-pressurized dome versus the upward force of the outlet-reduced pressure.
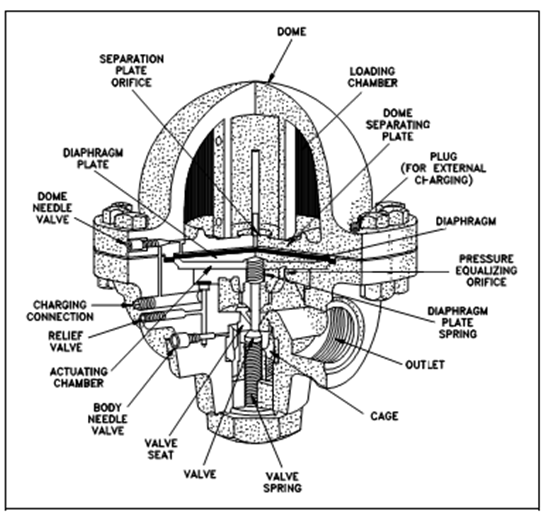
Figure: Non-Variable Reducing Valve
Non-variable reducing valves eliminate the requires for the middle auxiliary valve found in variable reducing valves through having the opposing forces react straight on the diaphragm. Thus, non-variable reducing valves are more responsive to large pressure differences and are less susceptible to failure than are variable reducing valves.