Applications
Aluminum, along with its low cost, low thermal neutron absorption and freedom from corrosion at low temperature, is ideally suitable for use in research or training reactors in the low kilowatt power and low temperature operating ranges.
Aluminum, commonly in the associatively pure (greater than 99.0 percent) 2S (or 1100) form, has been widely used as a reactor structural material and for fuel cladding and other purposes not including exposure to extremely high temperatures.
Aluminum along with its low neutron capture cross section (0.24 barns) is the preferred cladding material for pressurized and boiling water reactors operating in the moderate temperature range. Aluminum, in the type of an APM alloy, is commonly used as a fuel-element cladding in organic- moderated reactors. Aluminum has also been employed in gas-cooled reactors operating at low or moderately high temperatures. Commonly, at high temperatures, the associative low strength and poor corrosion properties of aluminum make it unsuitable as a structural material in power reactors because of hydrogen generation.High temperature corrosion and strength properties of aluminum could be raised through alloying, other than just at the expense of a higher neutron capture cross section.
In water, corrosion limits the use of aluminum to temperatures near 100ºC, unless special precautions are taken. Within air, corrosion limits its use to temperatures slightly over 300ºC. Failure is caused through pitting of the otherwise protective Al (OH)3 film. A presence of chloride salts and of a few other metals which form strong galvanic couples (for instance, copper) could promote pitting.
Aluminum is attacked through both water and steam at temperatures above about 150ºC, but this temperature can be raised through alloying along with small percentages of up to 1.0% Fe (iron) and 2.5% Ni (nickel). Those alloys are called as aerial alloys.A mechanism of attack is attributed to the reaction Al + 3H2O → Al (OH)3 +3H+ while the hydrogen ions diffuse by the hydroxide layer and on recombination and disrupt the adhesion of the protective coating.
Aluminum-uranium alloys have been used as fuel components in various research reactors. Enriched uranium is alloyed along with 99.7 percent pure aluminum to form the alloy.
Research has displays in which radiation generates changes in both annealed and hardened aluminum and its alloys. Yield strength and tensile strength rise along with irradiation. Data denotes in which yield strengths of annealed alloys are more affected through irradiation than tensile strengths.An yield strengths and the tensile strengths of hardened alloys undergo about the similar percent increase as a result of irradiation. The Irradiation tends to decrease the ductility of alloys. An unirradiated control specimen and Stress- strain curves for an irradiated are displays in Figure. Figure described the effect of neutron irradiation in increasing the yield strength and the tensile strength and in decreasing ductility.
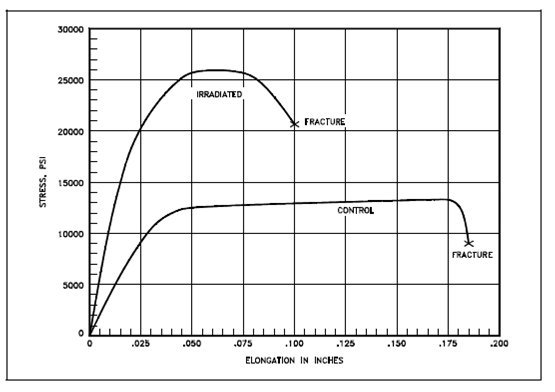
Figure: Effect of Irradiation on Tensile Properties of 2SO Aluminum