Steel making
Steel was first produced in China and Japan in about 600-800 AD. The process is fundamentally one of refining the pig iron acquired from the blast furnace. The pig iron refining consists of the percentage of reduction of manganese, carbon, silicon and other elements, and control of its composition via the addition of different elements. The molten metal from the blast furnace is transported in one of three types of furnace. The steel making furnaces are unwrap hearth, electric, or necessary oxygen. The name open hearth derives from the shallow heart shape such is open directly to the flames such melt the metal. Developed in the 1860s, the open-hearth furnace is being replaced by electric furnace and via the basic-oxygen process. These newer methods are more produce and capable in better quality steels.
The electric furnace was first introduced in year 1906. The source of heat is a carries on electric arc formed in between the charged metal and the electrodes. Temperature as high as 1925oC are produced in this type of furnace. There are mostly three graphite electrodes in direct arc electric furnace, and such can be as large as 750 millimeter in diameter and 1.5 to 2.5 meter in length. In the furnace their height can be adjusted that is depending upon the amount of metal current as well as water of the electrodes.
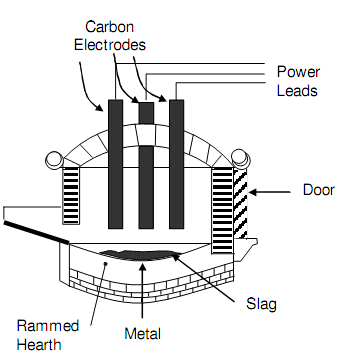
Figure: Direct Arc Electric Furnace
Steel scrap and a minute amount of limestone and carbon are dropped in the electric furnace via the open roof. Electric furnaces can also employ 100 percent scrap as its charge. The roof is after that closed and the electrodes are lowered. Power is turned on, and inside a period of about two hours the metal are melts. The furnace is titled and the current is shut off, the electrodes are elevated, and the molten metal is poured into a ladle that is a receptacle employed for pouring and transferring molten metal. Electric-furnace capacities range from 60 to 90 tons of steel daily. The produced steel is better than that of open-hearth or basic-oxygen process. Produced steel Quality is better than that of open-hearth or basic-oxygen procedure.
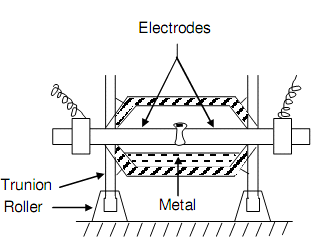
Figure: Indirect Arc Electric Furnace
The induction type electric furnace following figure is employed for smaller quantities. The metal is placed in crucible, and such made of refractory material and surrounded along with a copper coil throughout that alternating current is passed. In the charge the induced current melts the metal. These furnaces are utilized for re-melting metal also fore casting.
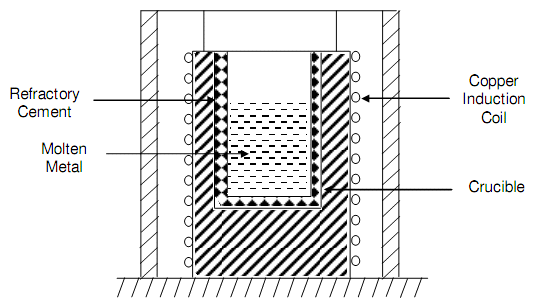
Figure: Induction Type Electric Furnace
The basic-oxygen furnace or BOF is the fastest and newest steel making procedure. Usually, 90 tons of scrap and 200 tons of molten pig iron are charged into a refractory lined barrel shaped vessel termed as converter. Pure oxygen is after that blown into the furnace for about 20 minutes beneath a pressure of about 1250 kPa, throughout a water- cooled lance, as represented in figure (b) of Basic Oxygen Process of Steel Making Illustrated through Various Operation. Fluxing agents, as like burnt lime are added with a chute.
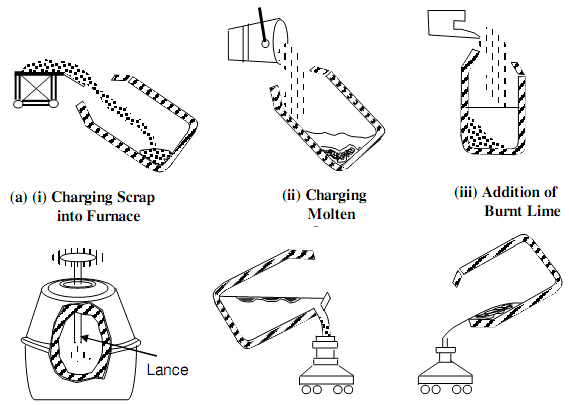
Figure: Basic Oxygen Process of Steel Making Illustrated via Various Operations
The vigorous agitation via the oxygen refines the molten metal with an oxidation process in that iron oxide is first generated. The oxide reacts along with the carbon in the molten metal, generating carbon oxide and carbon monoxide. The iron oxide is decreased to iron. The lance is concerned and the furnace is tapped through tilting it. In the vessel the opening is so specified that the slag yet floats on the top of the molten metal like seen in above figure (c). The slag is then removed through tilting the furnace in the opposite way.
The basic-oxygen furnace process is capable of refining 250 tons of steel in 35 to 50 minutes. Mostly basic-oxygen furnace steels such are of better quality then open-hearth furnace steels and comprise low impurity levels, are methods into plates, various structural shapes and sheets, like: I-beams and channels.
Steel might also be melted in induction furnaces from which the air has been removed, similar to the one shown in figure of Induction Type Electric Furnace. The vacuum melting produces elevated quality steels since the process removes gaseous impurities from the molten metal.