Iron Making
The three raw materials are charged into blast furnace by carrying them to the top of and dumping into the furnace. This principle was developed in Central Europe, and the first furnace started operating in the year of 1621.
The charge mixture is melted in a reaction at 1650oC with air preheated to about 1100oC and blasted into the furnace (hence the term blast furnace) through nozzles (or tuyeres). Although a number of reactions might take place, basically the reaction of iron oxide with carbon produces carbon monoxide, which in turn reacts along the iron oxide, reducing it to iron. Preheating the incoming air is necessary because the burning coke along does not produce sufficiently high temperature for the reactions to occur.
The molten metal accumulates at the bottom of the blast furnace, whereas the impurities float to the top of the metal. At gap of four or five hours, the molten metal is tapped, into ladle cars. Each ladle car might hold as much as 160 tons of molten iron. The molten metal at this stage has a typical composition of 4 % carbon, 1.5 % silicon, 1 % manganese, 0.04 % sulphur, and 0.4 % phosphorous, with the rest being pure iron. The molten metal is referred like a pig iron. Use of the world pig comes from the early practice of pouring molten iron into small sand molds, arranged as a litter of small pigs around a major channel. The solidified metal is called pig and is utilized in making iron and steels. The blast furnace is illustrated in Figure 1.
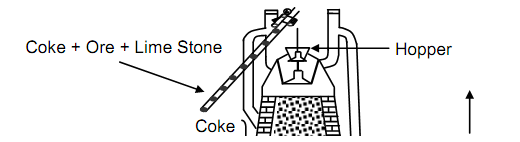
Figure: Blast Furnace