Aggregate Production Planning:
Aggregate planning is an integral part of the business planning process. All of the business organizations experiences time varying demand of its products. it leads requirement of aggregate plan that is a statement of its production rates, workforce level, and inventory holding based on estimates of the customer requirements and capacity limitations. Production rates refer to the number of units completed per unit of time (such as per hour or per day). Workforce level is refer to the number of workers required for production (production
= production rate × workforce level). Inventory holding is unused inventory carried over from the previous period. A manufacturing firm's aggregate production plan generally focuses on production rate and inventory holdings. Based on the broad, long term goals of an organization the aggregate production plan determines as to how organisation will work in future. For manufacturing companies, the aggregate plan links strategic goals and objectives with the production plans for individual products and specific components that go in to them. Here is formal statement of the aggregate planning difficulty: given the demand forecast Ft for each period t in the planning horizon that extends over T periods, determine the production level Pt, inventory level It, & workforce level Wt for periods t
= 1, 2, . . . , T that minimize relevant costs over the planning horizon. The form of aggregate plan varies from company to company. In some firms, it is a formalized report containing planning objectives and the planning premises on which it is based. In other companies, particularly smaller ones, the owner may make simple calculations of workforce needs that reflect staffing strategy.
The way of deriving the plan varies according to circumstances. One common approach is to derive it from the corporate annual plan, as illustrated in Figure. This figure shows the hierarchical planning process. A typical corporate plan contains a section of manufacturing that specifies how many units in each major product line need to be produced over the next 12 months to meet the sales forecast. The planner takes this information and attempts to determine how best to meet these needs along with available resources. Alternatively, some organizations combine output requirements into equivalent units and use this as the basis for aggregate planning. For instance, a division of Ford Motors can be called to generate a certain number of cars of all types at a particular facility. The production planner would then take the average labour hours needed for all models as a basis for the overall aggregate plan. Refinements to this plan, specifically model types to be produced, would be reflected in short-term production plans.
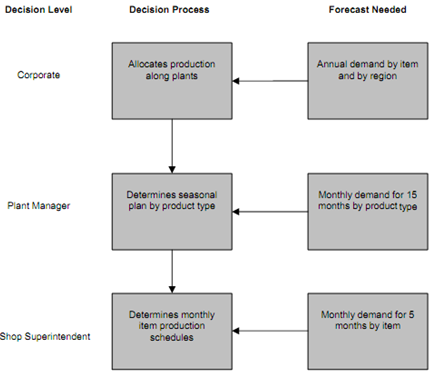
Figure: Hierarchical Production Planning Process
Another approach is to devolve the aggregate plan by simulating various master production schedules and calculating corresponding capacity requirements to see if adequate labour and equipment exist at each work centre. If capacity is insufficient, additional requirements for overtime, subcontracting, extra workers and so forth are specified for each product line and combined in to a rough-cut plan. Then this plan is modified by cut-and-try or mathematical methods to derive an ultimate and (one hope) lower cost plan.
Objectives
After studying this unit, you should be able to
- know about aggregate production planning environment, and
- learn aggregate production planning strategies.