Metallic pattern:
The metallic pattern plate is heated up to a temperature of 200 to 350 degrees based on the type of pattern. This is very essential that the pattern plate is consistently heated so that the temperature variation across the entire pattern is within 25 to 40 degrees based on the size of the pattern. A silicone agent is sprayed out on the pattern and the metal plate. The warmed pattern is safely fixed to a dump box, in which the coated sand in an amount greater than needed to form the shell of the essential thickness is already filled in.
After that the dump box is rotated in order that the coated sand falls on the heated pattern. The heat through the pattern melts the resin adjacent to it therefore causing the sand mixture to hold on to the pattern .
While a desired thickness of shell is attained, the dump box is rotated backwards through 180 degrees so that the excess sand falls back in the box, leaving the built shell intact with the pattern. The average shell thickness attained depends on the temperature of the pattern and the time the coated sand stay in contact with the heated pattern.
The shell along the pattern plate is kept in gas fired or electric oven for curing the shell. The curing of the shell might be done as per requirements just because over curing might be cause the mould to break down like the resin would burn out. The under curing might result in blow holes in the casting or the shell might break throughout handling because of the lack of strength.
Thus the shells prepared are combined together by either adhesive bonding or mechanical clamping. The resin utilized as an adhesive might be applied to the parting plane before mechanical clamping and after that allowed for 20 to 40 seconds for attaining the needed bonding.
As the shells are thin, they may need some outside support so that they might withstand the pressure of the molten metal. A metallic enclosure to nearly fit the exterior of the shell is perfect; however it is too costly and therefore impractical. On the other hand, generally, a cast iron shot is preferred as it occupies any contour with no unduely applying pressure on the shell. Along such a backup material, this is possible to decrease the shell thickness to an economical level.
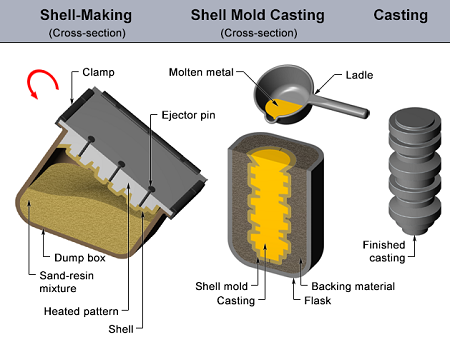
Figure : Steps in Shell Moulding