Deformation Processes
All plastic deformation processes exploit the ability of metals and alloys to change shape by plastic flow. The ability of the materials to deform without fracture varies widely. Bulk deformation processes cause the material to flow in all directions, whereas the ability to deform is expressed as workability; in sheet metal working processes deformation is essentially two-dimensional, and limits of deformation are referred to as formability. It is important to recognize that the limits of plastic deformation are the outputs of a system and these are greatly affected by the stress state prevailing in the process. If stresses are highly compressive (in other words, if a hydrostatic pressure component prevails), even a material of low workability can be deformed to a significant extent. Thus, process selection is based on knowledge of the workability or formability of the material and its variation with stress state, strain rate, and temperature. Because most processes involve sliding contact between the workpiece and a tool or die, the friction between the contacting surfaces affects material flow, the die pressures, and force and energy requirements. In most instances lubricants are chosen to minimise friction, but in some cases control of (and not necessarily low) friction is the aim. Lubricants also fulfill the important functions of reducing the die wear, cooling (or temperature control), and control of the surface topography of the product.
Table 2: General Characteristics of Bulk Deformation Processes
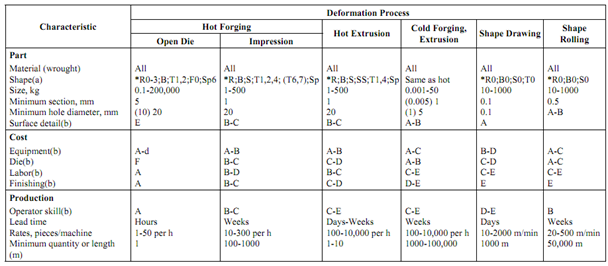