Casting Process
In the casting processes, shown in Table 1, a molten metal or alloy is poured into a mold, allowed to solidify and the part thus produced is removed from the mold. Very broadly, casting processes fall into two groups: expendable-mold and permanent-mold processes. Choice of process and mold material is greatly influenced by the melting point of the alloy. A very important issue is avoidance of voids (because of insufficient feeding of melt) and porosity (because of dendritic solidification and the existence of gases). Success depends, to a large extent, on the skill of the mold designer in choosing the position and size of sprue, runners, and risers, but there are very strong influences of the metal (alloy) and mold material. Solidification of the molten material on the mold walls closes passage of melt at a certain distance, and this leads to a minimum web thickness increasing with the width of the web. There are large variations in the fluidity of alloys; hence lower minimum thickness can be permitted with zinc, aluminum, and cast iron than with steel. Streamlined flow is helpful; thus sharp corners should be avoided. Thicker sections solidify last and must be fed sufficiently.
Table 1 : General Characteristics of Casting Processes
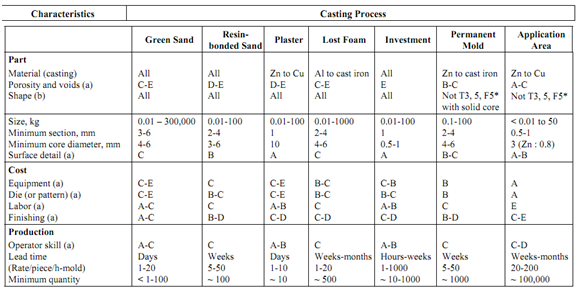
Table 1 presents general characteristics of casting processes. This table gives the comparative ratings of the various casting processes. Ratings with 'A' indicating highest value of the variable, 'B' the lowest (e.g. Investment casting gives very low porosity, produces excellent surface details involves moderate to low equipment cost, medium to high pattern cost, high labour cost, medium to low finishing cost and high operator skill.
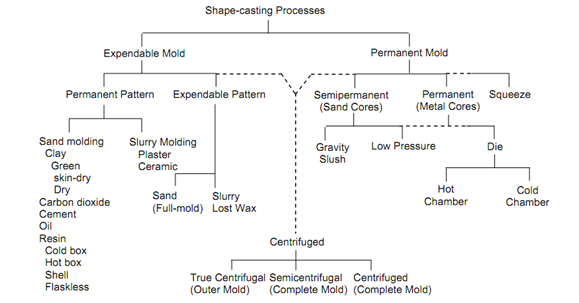
Figure 3 : General Classification of Shape-casting Processes