Screws and Dowels
Components of dies are held together through using socket head cap screws. The dowel gives and maintains accurate positioning of the elements, that is dowel prevents misalignment. To prevent projection of screw heads, the head is recessed in counter bored hole. Cap screws which are used to hold die elements are counter bored and 1/8 inch deeper than cap screw head. This permits additional material for die sharpening.
To position and hold die elements accurately, minimum one cap screw or dowel is essential for positioning. Designer can use two dowels but one can also use two or more cap screws. One cap screw is commonly enough for small elements, whereas in order to hold the die components at least two cap screws are needed for large components.
Generally, screws of diameter 3/8 inch are used for die elements of area up to
6 square inch and screws of diameter 1/2 to 5/8 inch are opted for heavy die elements. Dowel diameter is similar as that of cap screws. Dowels should be situated diagonally from each other and as farthest as possible to raise accuracy of location.
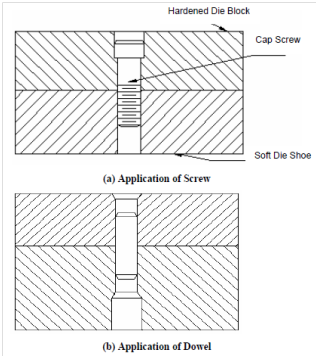
All the screws & dowels should be located at 1.5 to 2 times the diameter of screws or dowels from the elements edge. Screw and dowel hole should be placed near to the outer edge of the die block and as far as possible from blanking contour. Dowel holes extrude by the die elements so which dowels can be simply removed. The effectual thread depth for screws should be 1.5 times the screw diameter for common applications and two times the screw diameter while subjected to shock loads. Threading hard components should be prevented as far as possible. The die block should be drilled with clearance and counter bored to accept the cap screw. The thread should be cut in the die shoe. The application of screws and dowels has been display in Figures (a) and (b) correspondingly.