Simple Gear Pump:
There are various differences of gear pumps. A simple gear pump displays in below Figure consists of two spur gears meshing together and revolving in opposite directions inside a casing. Just a few thousandths of an inch clearance exists among the case and the gear faces and teeth extremities. Some liquid which fills the space bounded through two successive gear teeth and the case must follow along with the teeth as they revolve. While the gear teeth mesh along with the teeth of the other gear, the space among the teeth is decreased, and the entrapped liquid is forced out the pump discharge pipe. Since the gears revolve and the teeth disengage then the space again opens on the suction side of the pump, trapping new quantities of liquid and carrying it around the pump case to the discharge. Since liquid is carried away from the suction side then a lower pressure is created, that draws liquid in by the suction line.
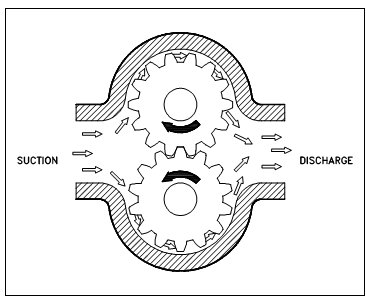
Figure: Simple Gear Pump
Along with the large number of teeth commonly employed on the gears, the discharge is associative smooth and continuous, within small quantities of liquid being delivered to the discharge line inside rapid succession. The space among the teeth is greater and the capacity increases for a given speed if designed with fewer teeth; therefore, the tendency toward a pulsating discharge rises. Within all simple gear pumps, power is applied to the shaft of one of the gears that transmits power to the driven gear by their meshing teeth.
There are no valves within the gear pump to cause friction losses as in the reciprocating pump. The high impeller velocities, along with resultant friction losses, are not needed as in the centrifugal pump. Thus, the gear pump is well suited for handling viscous fluids like as fuel and lubricating oils.