Synchro Equipment:
Remote indication or control might be obtained through the use of self-synchronizing motors, known as synchro equipment. A Synchro equipment consists of synchro units that electrically govern or follow the position of a mechanical indicator or device. The electrical synchro has two distinct benefits over mechanical indicators: (1) greater accuracy, and (2) simpler routing of remote indication.
There are five basic categories of synchros that are designated according to their function. The basic categories are: differential transmitters, transmitters, receivers, differential receivers and control transformers. Above Figure describes schematic diagrams used to display external connections and the associative positions of synchro windings. If the power needed to operate a device is higher than the power available from a synchro, power amplification is needed. A Servomechanism is a term that refers to a variety of power-amplifiers. These devices are incorporated into synchro systems for automatic control rod positioning in a few reactor facilities.
A transmitter, or synchro generator, consists of a rotor along with a single winding and a stator within three windings placed 120 degrees apart. While the mechanical device moves then the mechanically attached rotor moves. A rotor induces a voltage in every of the stator windings based on the rotor's angular position. Because the rotor is attached to the mechanical device and the induced voltage represents the position of the attached mechanical device. The voltage generates through every of the windings is utilized to control the receiving synchro position.
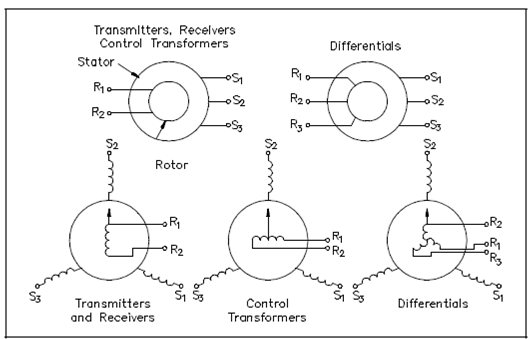
Figure: Synchro Schematics
The receiver or synchro motor is electrically same to the synchro generator. A synchro receiver uses the voltage producer through each of the synchro generator windings to position the receiver rotor. Because the transmitter and receiver are electrically same, the angular position of the receiver rotor corresponds to which of the synchro transmitter rotor. The receiver differs mechanically from the transmitter in which it incorporates a damping device to avoid hunting. Hunting refers to the overshoot and undershoots which occur as the receiving device tries to match the sending device. The receiver would go past the desired point slightly without the damping device, and then return previous the desired point slightly within the other direction. This would continue, through smaller amounts every time, until the receiver came to rest at the desired position. The damper avoids hunting through feeding a few of the signal back, therefore slowing down the approach to the desired point.
Differential synchros are used along with transmitter and receiver synchros to insert a second signal. The angular positions of the transmitter and the differential synchros are compared and the difference or sum is transmitted to the receiver. This setup could be used to give a feedback signal to slow the response time of the receiver, therefore giving a smooth receiver motion.
Control transformer synchros are used while only a voltage indication of angular position is desired. It is same in construction to an ordinary synchro except in which the rotor windings are used only to produce a voltage that is known as an error voltage. A rotor windings of a control transformer synchro are wound with several turns of fine wire to generates a high impedance. Because the rotor is not fed excitation voltage, the current drawn through the stator windings would be high if they were the similar as an ordinary synchro; thus, they are also wound along with several turns of fine wire to avoid excessive current.
In During normal operation, the outcome of a control transformer synchro is nearly zero (nulled) while its angular position is the similar as that of the transmitter.