Material Used For Composites
Composite represents a very broad range. From very common reinforced concrete to metal-metal fibre composites of high strength are in use. The strength of any particular material is governed by defects. These defects in solids are microcracks , dislocations or inclusions. It is intuitive of guess that number of these defects shall increase with size and surface area and hence material in form of thin wafers or fibres are likely to have less defects and hence better strength. Such material fibres and whiskers have certainly been developed. Whiskers are single crystals free of dislocations.
Glass fibres are very commonly utilized as reinforcing constituents. These fibres have high strength to weight ratios, high resistance to temperature (high and low), good dimensional stability, low water absorption and high electrical insulation. In addition the glass fibres are amenable to fabrication & cost less. Two kinds of glass fibres, recognized as E- glass and S-glass are commercially generated and are respectively utilized for high electrical insulation and mechanical strength. Glass fibres are generated by drawing from glass melt and are available in form of yarn, woven rovings and mats.
Carbon fibres are other commonly utilized reinforcement in plastic matrix. The fibres have high strength, low density, and high modulus of elasticity. Though, carbon fibres are much costlier.
Aramid fibers are basically aromatic polymide fibres and commercially available in two forms called as Kevlar 49 and Kevlar 29. Kevlar 29 is known for low density and high strength. Kevlar 49 has higher modulus of elasticity. Table describes mechanical properties of the fibres.
Boron fibres are yet another, known for its much superior stiffness, just next to graphite whiskers. Its density is comparable with E-glass.
Table: Comparative Mechanical Properties of Fibres
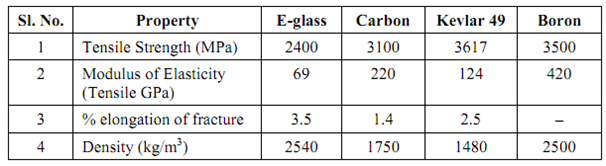
Different advantage of carbon fibres over E-glass might be seen in terms of strength, modulus of elasticity & density but carbon fibres are more brittle. Kevlar 49 contains ductility, higher strength and lower density but its modulus of elasticity is lower than that of E-glass. Glass fibres have distinct benefit of low cost. Boron fibres are costlier. Boron and carbon both fibres are susceptible to oxidation. Glass fibres do not oxidise. Glass fibre has the disadvantage of losing strength along temperature but boron & carbon fibres do not.
In single filament form Glass fibres are drawn from molten glass in a furnace. Large number of filaments is collected to make strands. The strands are converted in yarn & rovings. The strands are held together by resinous binder. Rovings are utilized to make glass fibre mats, which might be utilized to create composite with similar properties in a plane.
The properties of boron fibres, Kevlar 49, graphite fibre, S-glass, and E-glass fibres are shown in Figure. It might be noted that the tensile strength varies among 1700 and 3400 MPa while the fracture strain varies among 0.4 and 4.0%. Best combination of strength, modulus of elasticity & density is available in carbon fibres.
The carbon fibres are built from polymer fibres generated by throwing jet of molten polymer in coagulating bath. The fibres so generated are wound on frames, heated to 250oC to oxidise the fibres that shrink and turn black. These fibres are further carbonised in a furnace at about 1000oC and further heat treated at 1500oC and 1800oC for high strength and modulus of elasticity respectively. The polymer base of these fibres comprises acrylic polymers, polyacrylonitrite (PAN) or rayon. The PAN and rayon base fibres are costlier.
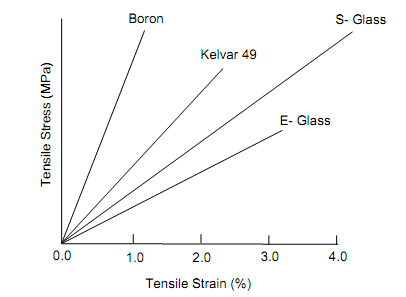
Figure: Properties of Some Fibres
Matrix materials of varied nature may be utilized with these fibres, glass, Carbon and Kevlar fibres are in common use. Carbon fibres may be utilized in plastics, carbon metals, glass and ceramics. Glass & carbon are brittle and metals are heavy in addition to they do not wet carbon fibre well. Ceramics contain very much different coefficient of thermal expansion and their best quality of high temperature resistance may not be used in association of carbon fibres. Plastics, so, are the best matrix material for carbon fibres.
The plastics utilized as matrix materials include, phenolics, polymides, polyesters thermoplastics and epoxies. However, these materials have great restriction in respect of temperatures. Polyesters and thermoplastics may be used only upto 100oC. Epoxies may be used upto 150oC. Phenolics may be utilized upto 250oC. However, Phenolics have poor mechanical properties. Polymides are better at temperature higher than 200oC but certainly not usable close to 400oC. Table compares two commonly utilized matrix materials with carbon, glass and kevlar fibres. Epoxies largely suit carbon fibres more than any other matrix material due to very good adhesion.
Table: Properties of Unfilled Cast Epoxy and Polyester
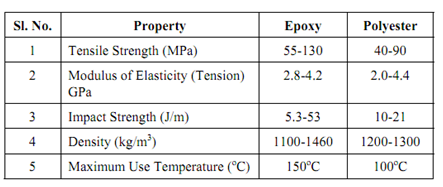
Epoxy resins have better strength, higher cost and utilized as matrix for carbon fibres and aramid fibres. As composites their distinctive applications are in marine, aerospace and automotive engineering, and carbon fibre in these areas reinforced composites are replacing metallic materials for their high strength/weight ratio. Along the length of fibres these composite may develop a tensile strength of about 1800 MPa with modulus of elasticity of 145 GPa. However, their percent elongation is limited to just 1.2%. Unidirectional composites have extremely low transverse strength and modulus of elasticity. In properties, Overall improvement is obtained by combining unidirectional laminates at various angles as shown in given Figure
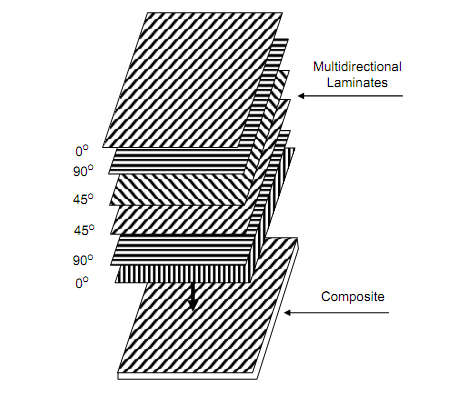
Figure: A Composite from Multidirectional Laminates
Generally, Glass fibres utilized with polyester as matrix may develop unidirectional tensile strength among 200 to 350 MPa with modulus of elasticity among 100 to 300 MPa. Generally higher weight percent of glass fibres built the composite stronger. As high as 80% fibre glass content is utilized in some cases. In all directions equal strength is obtained if chopped rovings are utilized as reinforcing material. But in this case strength is less than that with directional strands. Glass woven cloth sheets are also utilized as reinforcer in plastic but fibres lose strength at interlacing points because of interference. Boat hulls, structure and building panels are made in glass fibre reinforced polyester.