Ductility:
A percent elongation reported in a tensile test is described as the maximum elongation of the gage length divided through the real gage length. The measurement is determined as display in Figure.
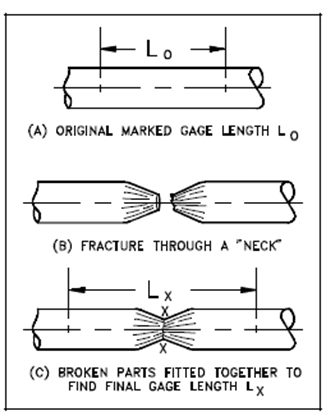
Figure: Measuring Elongation After Fracture
Percent elongation = final gage length- initial gage length/initial gage length (2-13)
= Lx - Lo/ Lo = inches per inch x 100 (2-14)
Decrement of area is the proportional reduction of the cross-sectional area of a tensile test piece at the plane of fracture measured after fracture.
Percent reduction of area (RA) = area of original cross section - minimum final area/ area of original cross section (2-15)
=Ao - Amin / Ao = decrease in area/ original area = square inches/ square inches
x 100 (2-16)
The reduction of area is reported as further information (for the percent elongation) on the deformational characteristics of the material. The two are used as indicators of ductility, an ability of a material to be elongated in tension. Since the elongation is not uniform over the whole gage length and is greatest at the middle of the neck, the percent elongation is not an absolute measure of ductility. (Since, of this, the gage length has always been beginning while the percent elongation is reported.) A reduction of area, being measured at the minimum diameter of the neck, is a better indicator of ductility.
Ductility is more generally described as the ability of a material to deform simply upon the application of a tensile force, or as the ability of a material to withstand plastic deformation without rupture. Ductility might also be by of in terms of crushability and bendability. Ductile materials display huge deformation before fracture. A lack of ductility is frequently termed brittleness. Commonly, if two materials have the similar strength and hardness, the one which has the higher ductility is more desirable. A ductility of several metals could modify if conditions are altered. A rise in temperature will increase ductility. A decrease in temperature will cause a decrease in ductility and modify from ductile to brittle behavior. Irradiation will also decrease ductility, as elaborates in another module.
Cold-working also tends to make metals less ductile. A Cold-working is performed in a temperature region and over a time interval to acquire plastic deformation, other than not relieving the strain hardening. Minor further of impurities to metals, either deliberate or unintentional, could have a marked effect on the change from ductile to brittle behavior. A heating of a cold-worked metal to or above the temperature at that metal atoms return to their equilibrium positions will raise the ductility of that metal. This procedure is known as annealing.
Ductility is desirable in the high temperature and high pressure applications within reactor plants since of the added stresses on the metals. A High ductility in these applications helps avoids brittle fracture.