Thread Cutting
Thread cutting is an important tasks carried out in most of the turning centres. Any thread form can be machined on a turning centre by following simple set rules. The actual thread form and proportions are standardised. These can be obtained from handbooks. Once the actual proportions of the expected thread form is known, it is necessary to convert this into a CNC program. In order to do that there are two things that need to be addressed:
(a) Specification of the depth of cut
(b) Following the thread form.
The thread form generally has considerable depth of material to be removed, which cannot be done in a single cut. Thus, it becomes necessary to determine the individual depth of cut that can be given. There are two ways in which the depth of cut in thread cutting can be given :
(i) Plunge feeding in which the form tool is moved in between cuts along the X-axis only to give the depth of cut . In this method, the tool since moves in only one direction, it will be centred in the thread form and both the cutting edges will be performing the cutting action. This means that the tool will have to be provided with a zero rake angle, which will increase the prevailing cutting forces and also lead to chatter. This will not provide good surface finish. Generally, this form is not preferred, though it is easy to program.
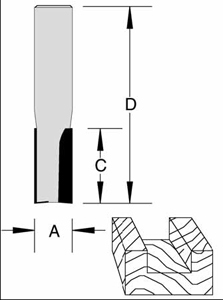
Figure 54 : Depth of Cut in Thread Cutting - Plunge Feeding
(ii) Compound feeding is the case when the tool is moved along both X-axes and Z-axes simultaneously for giving the depth of cut. The angle of movement will coincide with the angle of the thread. As a result only one edge of the tool will be cutting giving rise to a better cutting process. The finish achieved in this process will be good and is generally preferred. The tool will be positioned only along one edge as shown in Figure 55 depending upon the direction of the cutting.
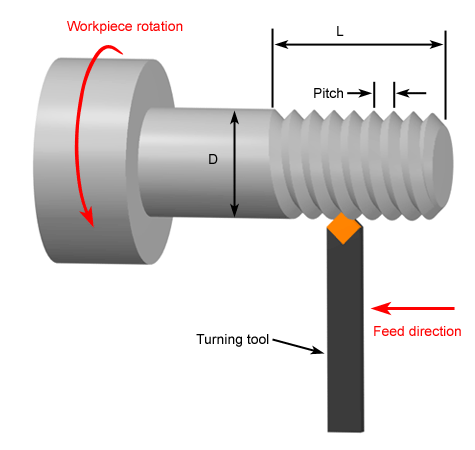
Figure 5.55 : Depth of Cut in Thread Cutting - Compound Feeding
The second care to be taken while thread cutting is that the tool should follow exactly the same path as followed in the first cut, thereby ensuring that correct thread is generated.
To ensure this, the tool motion for feeding will have to start exactly at the same point on the periphery for all the cuts. This needs synchronisation of spindle motion and feed motion, which is achieved by the use of G33 code. G33 is modal and, therefore, needs to be specified whenever it is to be applied.