Rockwell Hardness
Rockwell hardness is another method of hardness measurement, which like Brinell hardness, is very popular in engineering practice. In this method two types of indenter, viz., a Brale indenter in form of 120o diamond cone or steel balls of 1/16 in and 1/8 in diameter are used. These indenters are shown in Figure . Rockwell method differs from Brinell method because Rockwell hardness is not measured as ratio of load to indentation surface area. Instead, Rockwell hardness is measured on an arbitrary scale on which hardness number is inversely proportional to depth of indentation.
The method consists in seating the specimen on platform of the machine and then applying a minor load of 10 kgf on the specimen through the indenter. This minor load helps to seat the specimen and reduces the tendency of riding or sinking in. A major load which could be either 150, 100 or 60 kgf is then applied and the depth of indentation is automatically recorded as hardness number on a dial gauge. The dial of the gauge is divided into 100 division with each division representing a penetration of 0.002 mm. The dial scale is reversed so that a small indentation depth is read as high hardness.
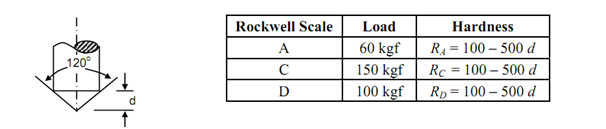
(a)
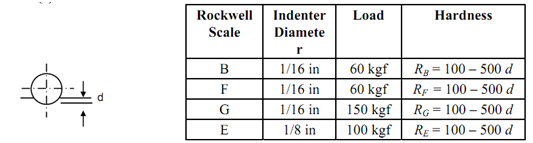
(b)Figure 31 : (a) Brale Indenter (Diamond Cone); and (b) The Spherical Ball Indenter of Steel, d is the Depth of Penetration
One combination of load and indenter will not be able to produce a wide range of hardness. Therefore, loads with three indenters are used in different combinations to provide wide range of measure hardness of several materials. Figure 31 shows the different scales of Rockwell hardness which is often expressed as R with a suffix A, B or C to indicate the scale. The scale (RC) is very commonly used for steel.
The Rockwell hardness is many times preferred over Brinell hardness because this test can be performed on very small parts in finished or unfinished condition. Since the indentation is very small, the finished surface is not spoilt and unfinished surface does not affect the indentation. Also since no measurement of indentation and consequent calculation are needed, the method is direct, fast and free from personal error.
However, several precautions regarding specimen and indentation have to the observed. The thickness of the plate specimen must be at least ten times the depth of indentation. This will avoid any effect of indentation to pass through the thickness. The distance between two adjacent impressions should at least be three times the size of indentation. The hardness read from indenting the curved surface should be corrected for curvature. The surface on which indentation is made must be clean and smooth and it should be well seated upon a clean platform. The rate of load application is controlled in Rockwell hardness testing machine and it is achieved by a dashpot adjustment corresponding to a standard rate of loading.