Brinell Hardness
This is a method of indentation hardness, which since its introduction in 1990 by J. A. Brinell has been extensively accepted for technological purposes. This method utilizes a steel ball of 10 mm diameter as indenter. The indenter is first placed upon the surface whose hardness is to be measured and then a slowly increasing load of 3000 kgf is applied upon the indenter. Whereas the load is eliminated an indentation is left upon the surface. For softer metals a lower load of 500 kgf is applied to avoid very deep indentation and for harder metals the steel ball is replaced by a tungsten carbide indenter so that indenter is not deformed. In each case the load is applied for a standard time, frequently 30 sec. Figure shows the indenter and indented plate.
The diameter of indentation is measured by low power microscope. From the knowledge of the indentation diameter and diameter of the spherical surface of the indentation (which will be equal to the diameter of the ball) the area of the spherical surface of the indentation can be calculated. Then the ratio of the load which caused the indentation to the area of indented surface is defined as the Brinell hardness number (BHN).
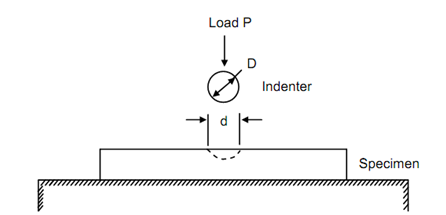
Figure : The Specimen and Ball Indenter for Brinell Hardness
If, P = Applied load, kgf,
D = diameter of the ball, mm, and
d = diameter of the indentation, mm.
then,
------------ (19)
Although, from the definition and Eq. (19) it is obvious BHN has units of kgf/mm2, this does not convey and physical meaning because the load P is not uniformly distributed over the indented surface.
The BHN value obtained for a material is fairly reproducible provided the load P and diameter D are same for each test. To obtain the same BHN at any other load the ratio d/D must be constant which requires that P/D must be constant. Thus for P = 3000 kgf, D = 10 mm, P/D = 30. Hence if a load of 2000 kgf is to be used the ball dia must be 8.15 mm, and for a 1 mm diameter indenter a load of 30 kgf must be used.
The calculated value of BHN may be slightly in error because of the assumption that the diameter of indented surface is same as that of indenter which is not exactly true. After the removal of the load, some elastic recovery takes place whereby the final diameter of the surface becomes different than ball diameter. For harder materials elastic recovery is greater than for softer materials.
An anomaly may arise in measurement of diameter of indentation diameter, d, due to localized deformation of metal in the region of indentation. Figure (a) shows the cross-section through indentation in a cold-worked metal. Because such a metal has little capacity to strain harden the metal has a tendency to pile up along the edge of impression. This behaviour is known as “pilling up” or “ridging”. Although the measured d is larger than actual diameter of indentation, yet the hardness is calculated on the basis of measured d as shown in Figure (a) because the ridge also carries part of the load.
Figure (b) shows the “sinking in” of an annealed metal. The depression around the edge of metal will apparently increase the diameter of the impression. To arrive at the true value of d, the indenter is often coated by a dye before making the indentation. The diameter then can be measured on the coloured ring.
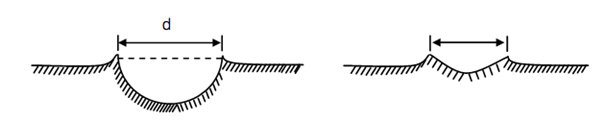
Figure 30 : Cross-section through Brinell Indentation on Two different Materials Showing
(a) Ridging; and (b) Sinking In
While making indentation on a plate specimen care must be exercised to avoid any interference between the indentation and the edge of specimen and the interference between two indentations. For this reason it is advisable that the centre of the indentation should be at least 1.5 D away from any edge. Same distance should be maintained between two neighbouring indentations. Similarly the thickness of the plate must be at least equal to the diameter of indenter so that the plastically deformed zone below the indentation does not interfere with the back surface.