Cupola Furnaces:
Cupola furnaces are the oldest kind of furnaces utilized in foundries. They are tall & roughly cylindrical and are most frequently used for melting iron & ferro alloys. Another layer of metal and ferro alloys, coke, & limestone are fed into the furnace from the top. Coke builds up 8 - 16% of the net charge to provide the heat that melts the metal. Limestone is added to react along impurities in the metal & floats to the top of the metal as it melts. Since in steel melting, this limestone/impurities combination is known as slag. By floating on top of the metal when it melts, the slag protects the metal from oxidation.
Cupola furnaces are lined along refractoriness, or hard, heat resistant substances such like fire, bricks, clay or blocks. The refractory protects the furnace shell from heat, abrasion and oxidation. Over time the refractory breaks down & eventually becomes part of the slag. Usually Cupola furnaces are associated to emissions control systems to capture air emissions. Usually, the air emission systems utilize either high energy wet scrubbers that utilize water to eliminate air pollution from the gas stream or dry baghouse systems that utilized fabric filters to capture the emissions.
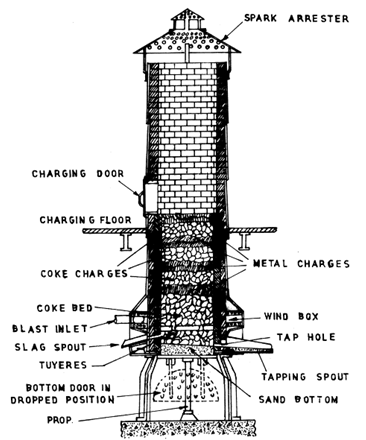
fig Cupola
The cupola furnace is build up of a vertical steel shell, 6-12 mm thick lined along refractory material down the entire length. Generally the lining is thicker in the lower region that means beneath the charging door where the temperatures encountered are greater than in the upper region. For combustion a constant volume of air is attained from a motorized blower of the positive displacement kind. The air is carried from the blower by a pipe is known the windpipe primary to a circular jacket around the shell and then into the furnace through a number of openings is known as tuyeres. Generally these tuyeres are 4, 6 or 8 in number based on the size of the cupola. The joint area of air inlets or tuyeres must be about one-fourth of the cupola plan area. The height of the tuyeres from the bed of the cupola is around 450-500 mm. Opposite of each tuyeres a little window with mica covers builds the inspection of fire conditions possible. At the bottom of the bed a spout is known as the tapping spout is provided for the molten metal. Opposite this tap hole and rather above there is another hole known the slag hole that enables the slag to be taken out.