Principles of MRP:
A material requirement planning is concerned primarily with the scheduling of activities and the management of inventories. It is specifically useful where there is a need to generate components, items or sub-assemblies which themselves are later utilized in the production of a final product or, in non-manufacturing organisations, where the provision of a transport or service for a customer necessitates the use or provision of certain subsystems. For example, it may be used when a customer orders a computer from a manufacturing organization, which must first manufacture or obtain various components which are used in the final assembly of that computer for that customer. Likewise, in treating a patient in a hospital, e.g. for a major operation, the hospital should, provide accommodation for the patient, diagnostic tests, anesthetics and post-care facilities as well as surgical facilities so that the patient's total requirements are satisfied. In these two cases the product or service requested by the customer may be seen to be the final output of the system, which derives from certain lower-level provisions. These lower-level provisions are considered to be dependent on the customer's final requirement. Given a measure or forecast of the total number of customers, the demand at lower levels may be obtained. The Materials Requirements Planning technique is used precisely for this purpose. It takes as one of its inputs, the measured or forecast demand for the system's outputs. It breaks down this demand into its component parts, compares this requirement against existing inventories, and seeks to schedule the parts required against available capacity. The MRP procedure generates a schedule for all component parts, if essential through to purchasing requirements, and where appropriate shows expected shortages because of capacity limitations. The basic procedure is illustrated in Figure. This procedure is undertaken on a repetitive basis. The explosion and scheduling procedure starts to be repeated at regular intervals, perhaps corresponding to the intervals at which demand forecasting is undertaken or as and while required as a result of changes in known demand. The use of this procedure involves considerable data processing, even for comparatively simple availability of cheap computing power in the organizations.
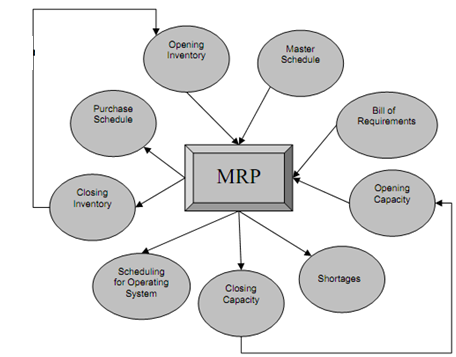
Figure: Fundamental Structure of Material Requirement Planning Procedure