Stress Rupture
In a typical creep test to establish creep curve emphasis is on strain measurement and stress is so chosen that minimum strain rate is attained. The total strain in such tests seldom exceeds 0.5% and time required for completion is in the range of 200 to 10,000 hours. The results of such experiments can be directly used in situations where creep deformation may be tolerated but fracture must be prevented. Moreover, the long time consumed in performing such tests may impede technological development. To cut short this time stress-rupture tests in which specimens fail by rupture have been developed.
The basic information that is obtained from the stress-rupture test is the time to cause failure at a given nominal stress for a constant temperature. The stress rupture curves are obtained by plotting rupture stress against time of rupture. The strain at rupture can be as high as 50% and time required may not be more than 1000 hours. The results of such tests can be directly used where creep deformation is tolerated but fracture is to be prevented.
The drawback with such a test is that at higher temperature some metallurgical changes may take place which change the slope of the straight line (on log-log scale) as shown in
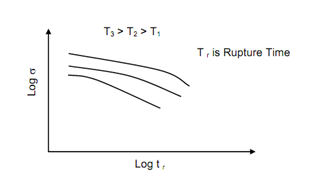
Figure: Stress Rupture Curves