Creep and Creep Curves
Theoretically speaking at any temperature a material will progressively deform under a constant load even if the stress is below yield. However, such deformation is negligibly small.
At high temperature the progressively deformation of a material under a constant stress is termed as creep and can become quite appreciable depending upon the combination of temperature and stress. The deformation of material in laboratory is mostly measured as strain suffered by tension specimen. The temperature at which creep becomes appreciable is half of the melting point temperature on absolute scale and is known as homologous temperature.
The creep experiments can be performed in simple machines that use dead weights and lever for loading the tension specimen. The specimen is surrounded by a furnace whose temperature can be controlled and recorded accurately alongwith elongation of specime.
Such an arrangement is shown in Figure (a) without furnace. Though not exactly true

Lever P
Materials Applications
the actual complicated arrangement for measurement of deformation of creep specimen may be like one shown in Figure (b): (a) Schematic of Creep Testing Equipment; and (b) An Arrangement for Measuring
The creep curves are plotted between strain and time for given stress and temperature. One typical curve is shown in Figure 44 for constant stress σ and temperature T.
To start with the specimen is loaded at point O which corresponds to zero strain and zero time. Immediately after application of stress the specimen suffers from elastic strain upto point A. As the time passes the specimen continues to extend with decreasing rate upto point B and with a constant rate from B to C. From point C the rate of increase of creep strain increases upto point D where the fracture or rupture takes place.
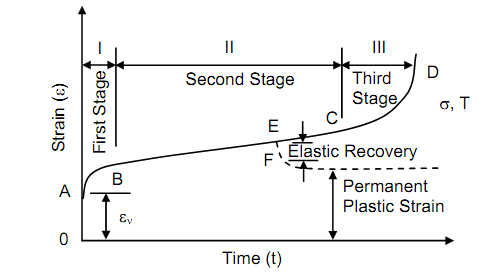
Figure : Characteristic Creep Curves at Stress and Temperature T
Although the description of creep curve appears to be quite simple, the collection of data involves complicated control, measurement and recording system. The important point to note is that the total time required in the creep curve may be very large, ranging from a few months to as long as 10 years. The instruments are supported to be working throughout his time. Generally a battery of machines is required to make simultaneous studies at different temperatures and stress levels.
A creep curve is conveniently divided into three stages. The stage of primary creep extends from point A to B, this covers a small part of total period. The creep during this stage is often referred to as transition creep and rate of creep decreases because of strain hardening of material.
From B to C, it can be seen that rate of creep is constant. This is known as stage II or creep and is identified by its constant rate. During this stage minimum constant creep rate is attained. This steady state creep is the result of balance between two effects of strain hardening and softening due to temperature. In service conditions most machine parts which are required to have infinite life work in secondary creep zone.
The final or tertiary creep from point C is marked with increasing creep rate ultimately culminating into rupture or separation of specimen into two pieces. This is termed stage III of creep. It may be pointed out there that during tertiary creep the necking also takes place which increases effective stress and thus rate of strain also increases.
If creep load is removed at any point like E during stage II then immediate elastic recovery takes place as shown from E to F. This is followed by a gradual strain recovery to permanent strain which does not recover at all.