DC motor
Magnetic fields can generate considerable mechanical forces. These forces can be harnessed to perform the work. The device which converts direct current energy into the rotating mechanical energy is a dc motor.
Motors can be microscopic in size, or of the size of the house. Some tiny motors are being considered for use in medical devices that can actually circulate in the bloodstream or be installed in body organs. Others can pull the train at freeway speeds.
In the dc motor, the source of electricity can be connected to a set of coils, generating magnetic fields. The attraction of opposite poles, and the repulsion of like poles, can be switched in such a way that a constant torque, or the rotational force, results. The greater the current which flows in the coils, stronger the torque, and more electrical energy is required.
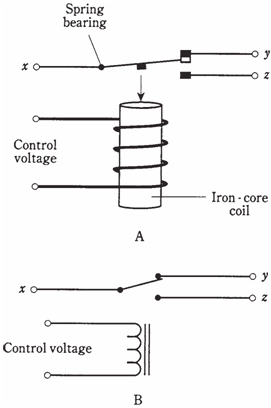
Figure-- At A, pictorial diagram of a simple relay. At point B, schematic symbol for the same relay.
Figure given above is a simplified, cutaway diagram of a dc motor. One set of coils, called as armature coil, goes around with motor shaft. The other set of coils, known as field coil, is stationary. The current direction is reversed periodically during each rotation by the means of the commutator. This keeps force going in the same angular direction, such that the motor continues to rotate rather than oscillating. The shaft is carried along by its own inertia, such that it does not come to a stop during those instants when current is being switched in polarity.
Some dc motors can be used to generate direct current. These type of motors contain permanent magnets in the place of one of the sets of coils. When shaft is rotated, a pulsating direct current appears across the coil.