Polycrystalline Diamond (PCD)
It is the hardest material we know of and has superior abrasive resistance to any other cutting material. Due to it's extraordinary hardness and wear resistance, PCD cutting tips retain their sharpness even in demanding applications, running up to cutting speeds of 1500 m/min. and beyond. As a result, PCD inserts provide up to 100 times the tool life of carbide. Excellent for light roughing and high speed finishing on turning, boring and milling operations. However, diamonds are found to be unsuitable for machining of ferrous materials especially at temperatures above 700oC, as during machining, diamond converts to relatively weakly bonded graphite. This leads to diffusion wear during machining as carbon contain a strong affinity for iron, leading to formation of iron carbides which wears away the cutting tip.
The PCD can be produced to different grades with varying toughness and hardness. They are available in three grain sizes termed fine, medium and coarse. The fine grain PCD is more wear resistant and less resistant to shock than the coarse grained one. The medium grained PCD has properties in between other two.
Table 1 : Applications of Various Cutting Tools
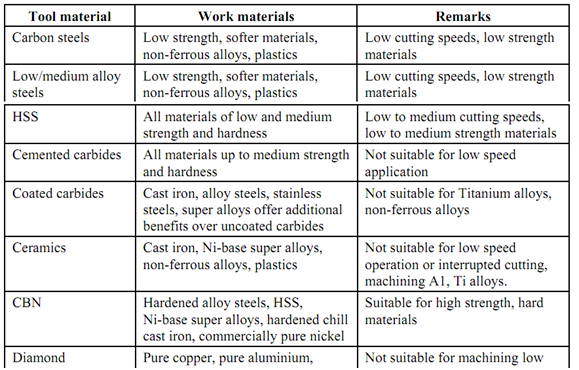
PCD inserts provide premium performance mainly in the machining of
- Highly abrasive alluminium alloys with higher silicon content,
- Low tensile strength non-ferrous or non-metallic materials,
- Magnesium, and
- Copper, zinc and their alloys.