High Speed Steel
Taylor and White developed this new generation tool material at the turn of the twentieth century. They were able to considerably enhance the cutting speeds by three to five times (about 0.5 m/s) of the cutting speed attainable at that time, using carbon tool steels. Due to this high cutting speed capability they were termed as high speed steels or HSS.
This class of tool materials have significant quantities of, molybdenum, tungsten chromium & vanadium. The complex carbides of tungsten, molybdenum and chromium distributed all through the metal matrix gives very good hot hardness and abrasion resistance. The major alloying elements that contribute to the hardness are tungsten and molybdenum. Tungsten is costly, whereas molybdenum is cheap but has higher toughness. For similar hardness, less amount of molybdenum requires to be added, though more care needs to be exercised in hardening as decarburizing takes place in molybdenum steels. Also they contain a narrow temperature range for heat treatment. Molybdenum tool steels are more admired.
The major advantages of high speed steels are in their good wear resistance, high hardness, high toughness and reasonable cost. Toughness of high speed steels is highest among all of the cutting tool materials. Therefore they are quite extensively utilized in interrupted cutting such like in milling. The hardness of HSS falls quickly beyond 650oC as illustrated in Figure 2 and therefore they are restricted to lower cutting speeds of the order of 0.5 to 0.75 m/s.
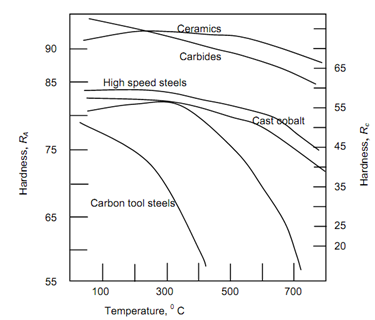
Figure 2