Coated Carbides
Coating carbide tip/inserts with 4-10 microns (0.004-0.01 mm) of titanium carbide coating enhances wear resistance to triple the tool life. Coated carbides also permit operation at 40 per cent higher cutting speed. A mixture of vaporized titanium tetrachloride, hydrogen and methane is passed over a cooling system into the retort. The titanium carbide layer formed on the surface is bound metallurgically to the cemented carbide tip within. This cycle of vapour deposition coating takes nearly eight hours.
Resharpening of the carbide tips involves lapping on expensive diamond wheels. Consequently, it is much more economical to use clamped carbide tip/insert in a steel holder. The inserts are provided with more than one cutting edge. After wear the insert can be indexed to bring a new cutting edge in the operating position. Consequently, these inserts can be thrown away after wear instead of resorting to expensive lapping on diamond wheels. Figure 3 shows how the coating on tools will improve the wear resistance.
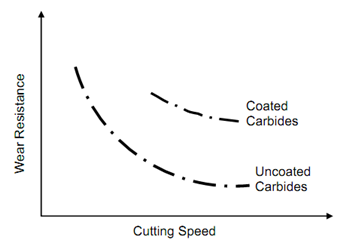
Figure 3 : Effect of Coating Carbides