JIT Layout and Design Flows:
JIT requires the plant layout to be designed to ensure balanced work flow with a minimum of work-in-process inventory. Each of the workstation is part of a production line, whether or not a physical line in fact exists. Capacity is balanced by using the same logic for an assembly line, and operations are linked through a pull system. Additionally, the system designer must visualize how all of the aspects of the internal and external logistics system tie to the layout.
Preventive measurement is emphasized to make sure that flows are not interrupted by downtime or malfunctioning equipment. Preventive maintenance involves periodic inspection and repair designed to keep a machine reliable. Operators may perform much of the preventive maintenance work because of familiarity with their simple machines. JIT philosophy favours various simple machines rather than one large complex machine.
The reduction in setup and changeover times is essential to achieve a smooth flow. Figure shows the relationship among the lot size and setup costs. Under a traditional approach, setup cost is treated like a constant, and the optimal order quantity is illustrated as six. Under the Kanban approach of JIT, setup cost is treated as a variable and the optimal order quantity is eliminated. In the figure drawn, the order quantity has been eliminated from six to two under JIT by employing setup-time-saving procedures. This organization shall ultimately strive for a lot size of one.
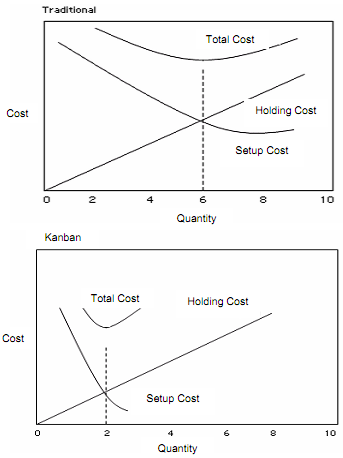
Figure: Relationship between Lot Size and Setup Cost