Components of Computer Integrated Manufacturing
Setting system boundaries for a CIM project may at first appear to be concerned only with the engineering design & actual manufacture of the products. When the integration of these two components is a main task which is not satisfied in mostly facilities, CIM goes beyond these activities. Given figure shows graphically what is involved in computer integrated manufacturing.
So far as plant itself is concerned, there are five main components:
Computer Aided Engineering (CAE)
CAE encompasses CAD, NC programming, tool and fixture design, quality control (QC) planning, and process planning. This later on area that ties CAD and CAM together and when automated is called computer aided process planning (CAPP).
Operations Management
Operations management governs the acquisition of all materials needed for product manufacture; since a cost effective system is required, it is mandatory to include cost accounting. Production planning and control is needed to ensure that parts are routed in an efficient manner to keep equipment busy as well as to ensure that customers needs are satisfied. Shop floor controls are required to make sure that production data is available to production planning and control as well as to allow planned sequencing to be effected on the shop floor.
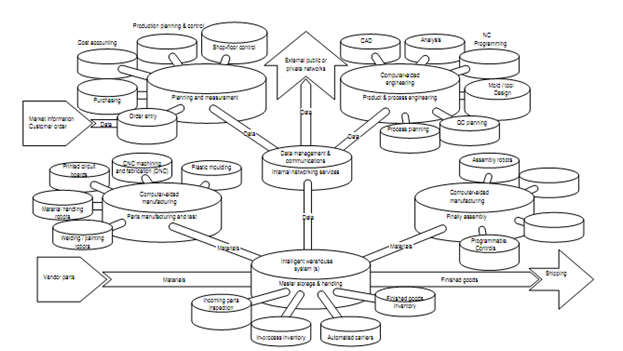
Figure: Structure of CIM
Computer Aided Manufacturing - Manufacturing and Test
Parts have to be manufactured and tested. A major point is made in given figure that must be exemplified at this point. Several people think that computer aided manufacturing is for chip-cutting part only - those parts that are machined in same fashion. It is not true, as it cannot be stressed too forcefully. Several activities associated to manufacturing of PCBs (Printed Circuit Board), controlling non- traditional machines (Electrical Discharge Machine, Electrochemical Machines etc.) and several precision operations have been using the salient features of CAM.
Computer Aided Manufacturing - Assembly and Test
Assembly, inspection and packing are the important features of CAM. They play a vital role in the success of the implementation of CIM systems.
Intelligent Warehousing
The last component of the CIM encompasses automatic storage & retrieval of materials and components, & finished goods. This takes into consideration the incoming materials, products in addition to the work-in-progress (WIP).
Finally to permit all the components to work as an integrated system, we have to integrate the five components with a network system as exemplified by the data management and communications modules illustrated in given figure. Standards have been evolved for this function, but the information flow in CIM is a main problem, which is yet to be handled in an effectual manner.
In continuation to the systems approach, it is essential to break the system into components for initial analysis. Actually the overall systems approach would be applied to the six major components as mentioned before, including the component of data management and communications. Analysis of the whole system is a difficult & tedious process as compared to the analysis of individual modules. This problem attains a complex magnitude, while one considers the integration of computer systems for design and manufacturing.
After the initial analysis of the components, the integration aspect is taken up. This is done through a networking scheme along with a smart database able to handle design, manufacturing, and planning. To attain this, a hierarchical computer structure should be employed. The manufacturing database remains at the top of the hierarchy followed by equipment controlling and data-gathering systems.