Channel Induction Furnace:
For bigger quantities, channel induction furnaces are utilized. In these furnaces the copper coils are surrounded through inductors to promote metal melting. Commonly channel furnaces are utilized to hold the molten metal prior to casting. In cored induction furnace, induction coil is fundamentally immersed in the metal bath. Electromagnetic induction pumps liquid metals by channels around the coil and simultaneously secondary currents (which behaves as the heating source) are induced in the liquid metal around the core .The chief disadvantage of the cored induction furnace is that it needs a liquid metal beginning charge so it is not appropriate for intermittent operation. The cored furnace is utilized primarily for non-ferrous metals in applications where comparatively long periods of constant operations are wanted. Induction channel furnaces were utilized initially as molten metal holders, but are used for some melting applications as well now.
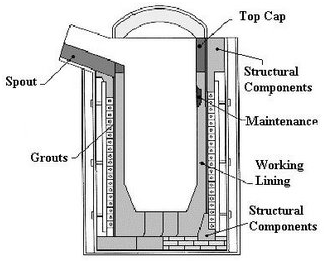
Figure : A Channel Induction Furnace
While all of the channel furnaces are line frequency, coreless furnaces might be line frequency (60 Hertz), medium frequency (200 Hertz through 1,200 Hertz) or high frequency (over 1,200 Hertz). Line frequency furnaces are slower to begin from a cold charge resulting in raising preference for medium & high frequency units. Improvements in frequency converters and lower expense have also aided acceptance.