Tempering and Stablisation
Tempering of tool steel is again an important step in heat treatment. The quenching of such steels causes the existence of untempered martensite, retained austenite and carbide in the structure. This happens because of finer changes in composition do not permit to establish correct austenising temperature. Tempering besides removing these structural deficiencies also help induce secondary hardness. Figure shows the presence of secondary hardness manifested by increased hardness at certain tempering temperature in case of high alloy steels. Both medium and high alloy steel decrease in hardness respectively upto about 460oC and 500oC and thereafter they increase in hardness. High alloy steels show greatest increase in hardness with increasing tempering temperature.
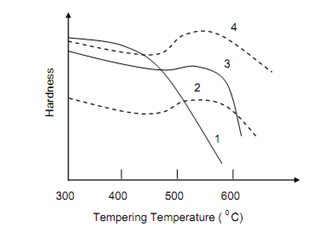
Figure: Tempering Characteristics of Tool Steels
After tempering initially the treatment is repeated two or three time in multi-tempering practice. Such treatment stabilises the microstructure by reducing the amount of retained austenite. Yet another method of stabilization is to cool the tempered steel to subzero temperature by placing it in solid carbon dioxide (– 75oC) or dipping it in liquid nitrogen (– 196oC).
Normalised quenched, tempered and stabilised tool steel possesses maximum hardness, wear resistance and dimensional stability.