Cylinder Series Test
A series of round bars of different diameters are austenised and quenched in oil or water. The bars are long enough so that the cooling of section at the middle of the length is not affected by the ends. After hardening each bar is cut into half and hardness measured at various points along a diameter. The graph between hardness and distance from the centre is then prepared .From this graph the diameter at which 50% of the structure is martensite is determined. When this graph the diameter is plotted against bar diameter, it becomes possible to determine the bar diameter in which 50% martensite would form at the centre. This is called critical diameter for that quenching medium. Since the rate of cooling is less for an oil quench than for water quench, the critical diameter, of any steel will be less for oil quenching than for two water quenching. Severity of quench is an index that quantitatively defines the quenching condition. This index denoted by H is defined as following ratio.
H = Heat transfer coefficient between steel and fluid/ Thermal conductivity of steel
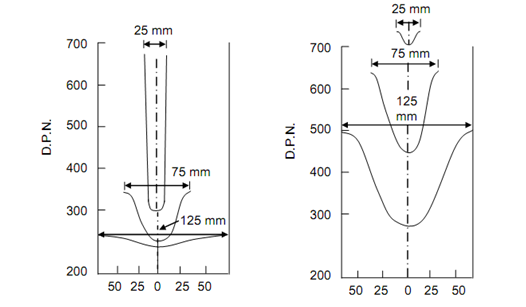
Figure: Variation of Hardness with Depth in Water-quenched Cylindrical Bars of
(a) Plain Carbon Steel, (b) 1% Cr-V Alloy Steel
Naturally, while H → ∞ it represents the severest condition of quench, meaning that surface of steel immediately reaches the temperature of the quenching medium. The critical diameter for such an ideal and unrealisable condition is called as ideal critical diameter. For infinite H-value the critical diameter & ideal critical diameter will be same. For other H values the critical diameter will be smaller. Figure shows the relationship between critical and ideal critical diameters for various H-values. Table explain relative values of H that may be obtained in several quench media under different condition with value of one for still water as base.
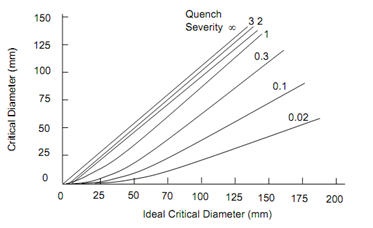
Figure: Relation between Critical Diameter, Ideal Critical Diameter and Severity of Quench
Table: Relative Quench Severities
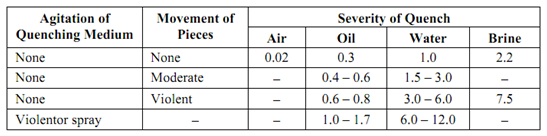