Cement Concrete Flooring
This kind of flooring is most generally used for residential, commercial and even industrial building, since it is moderately cheap, quite durable and simple to construct. The floor consists of two elements, which are:
(a) Base concrete, and
(b) Topping or wearing surface.
The two elements of the floor could be constructed either monolithically (i.e. topping laid immediately after the base course is laid) or non-monolithically. While the floor is laid monolithically, good bond among the two elements is acquired resulting in smaller whole thickness. Therefore, such a construction has three disadvantages. These are
(a) The topping is damaged during subsequent operations,
(b) Hair cracks are developed because of the settlement of freshly laid base course which has not set, and
(c) Work progress is slow because the workman has to wait at least till the initial setting of the base course.
Therefore in most of the cases, non-monolithic construction is preferred. First of all, a surface of the ground for receiving the floor is leveled, rammed and well-watered. Upon the above prepared surface of the ground, a 15 cm thick layer of broken stones or hard bricks is evenly spread and consolidated, given that the ground is made up of loose or soft soil. This sub-base or subgrade so prepared is also called as hard core. There by, a layer of lime concrete (1: 2: 4), about 15 cm thick is laid on the hard core or straight on the surface of the ground if made up of good soil. Essential slope is giving to the surfaces of lime concrete. To facilitate the washing down of the finished floor; generally a slope 1 in 120 to 1 in 240, is enough for inside floors and a outward slope of 1 in 36 to 1 in 40 is recommended for bath rooms and verandah floors. The lime concrete layer should be watered and well rammed for two days and on the third day the topping concrete should be laid.
Although the base concrete has hardened, its surface is brushed with stiff broom arid cleaned thoroughly. It is wetted the past night and excess water is grained. The topping is then laid in square or rectangular panels, through use of either glass or plain asbestos strips or through use of wooden battens set on mortar bed. The panels might be 1 × 1 m, 2 × 2 m or 1 × 2 m in size. The topping consists of 1: 2: 4 cement concrete, laid to the desired thickness (commonly 4 cm) in one single operation within the panel. Alternate panels are laid first. Prior to laying the concrete within the panel, a coat of neat cement slurry is applied. This cement slurry laid on rough finished base course ensures proper bond of topping along with the base course. Glass strips or battens should have depth equivalent to thickness of topping. Topping concrete is spread evenly along with the help of a straight edge, and its surface is by tamped and floated with wooden floates till the cream of concrete comes at the top.
Steel trowel is used for finishing and smoothing the top surface. Additionally troweling is done while the mix has stiffened. Dusting of the surface along with neat cement and then troweling results in smooth finish at the top. Other alternate layers are then laid after 72 hours, so that initial shrinkage of already laid panels takes place, thus eliminating the cracks. The prepared surface is protected from sunlight, rain and other damages for 12 to 20 hours. A surface is after that properly cured for a period of 7 to 14 days. While monolithic construction is laid, the topping is laid 1 hour to 4 hours after placing the base concrete. Figure 3 shows details of concrete flooring.
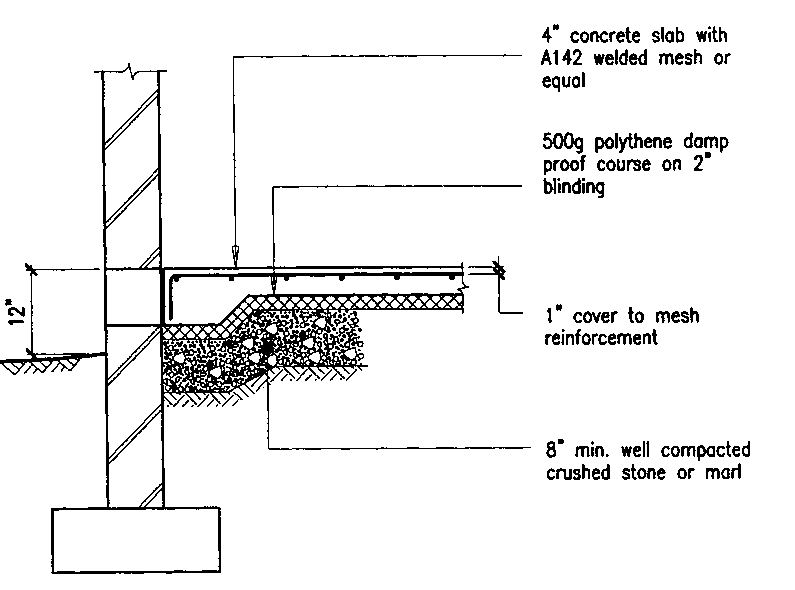
Figure : Concrete Flooring Details
In industrial building, hard wearing surface is sometimes needed. This could be achieved through applying granolithic finish over the concrete topping elaborates above. Granolithic finish consists of rich concrete made along with extremely hard and tough quality coarse aggregate (like as granite, basalt, quartzite etc.) graded from 13 to 240 no. I.S. sieve. The concrete merge proportion varies from 1 : 1 : 2 to 1 : 1 : 3 for heavy duty floors to 1 : 2 : 3 for public buildings. The thickness of finish might be minimum 25 mm while laid monolithically along with the top concrete, and 35 mm while laid over hardened surface. Therefore, for public buildings like as schools, hospitals etc. the thickness of the finish might be 13 mm to 20 mm using little size aggregate; If exceptionally hard surface is needed, sand might be replaced through fine aggregate of crushed granite, and/or abrasive grit might be sprinkled uniformly over the surface at the rate of 1.5 to 2.5 kg/sq m, during floating operation.