Solution Methodology
The process for finding the "operation allocation priority index" of a part kind can be illustrated as:
In machine loading problems, due to the availability of optional operations of part types, decisions are to be made for allocating operations on the machines. Following notations & definitions are to be introduced to describe the formulation of "operation allocation priority index" (after this termed as priority index "PI"):
- Operation Allocation: Operation allocation refers to the assignment of an operation of a part type on a machine.
Opom - operation "o" of part type "p" has been allocated to machine "m".
- Set of Operations Allocation: A set of operations allocation of a part type is described as the collection of distinctive operations allocations on the machines. The cardinality of this set is similar as the total number of operations of that part type.
ASp q = qth set of operations allocation of part type "p"
where "q" is the index for set of operation allocation number,
q = 1, 2, . . . , qmax.
- A set of operations allocation is represented like
AS pq={O p1m , O p2m , O p3m , . . . , O pOpm ''}
∀ m ,m', m'', . . . m''' ε {m}, where m =1 to M and m corresponds to o.
If a part type "p" contains op operations & if operation "o" might be allocated on qmax number of machines then the entire number of set of operations allocation (qmax) is given by
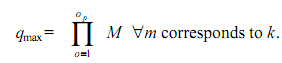
For instance, the part type "7", contains 3 operations, where operation 1 might be allocated on 3 machines, operation 2 on 3 machines & operation 3 on 1 machine. Thus, the entire number of sets of operation allocation that might be formed is:
(1)
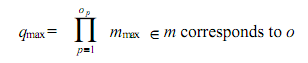
here mmax is the maximum number of machine on which the operation of the part type might be allocated.
For 0 = 1, m = 2, 3, 4, mmax = 3,
For 0 = 2, m =1, 2, 3, mmax = 3,
For 0 = 3, m =1, mmax = 1,
For 0 = 1, mmax = 3,
For 0 = 2, mmax = 3,
For o = 3, mmax = 1, and
Op = 3
∴ nmax = 3 × 3 × 1 = 9 .
The several set of operation allocation for this case are :
AS17 = {O127 , O217 , O34 7}
AS2 7= {O137 , O217 , O347 }
AS3 7= {O147 , O217 , O347 }
...............................
...............................
AS9 7= {O147 , O237 , O347 }.
- BP is the batch size of part type "p"
- tcopm is the unit processing time of operation "o" of part type "p" on machine m, ∀ "o" corresponds to "m".
- tcopm is the number of tool slots needed for carrying out oth operation of pth part type on mth machine, ∀ "o" corresponds to "m".
- IP is the position of part type p in the part type sequence, p = 1 to P and Ip = 1 and Ip.
- Machining Time Index: equivalent to each operation allocation of a part type on machine, the machining time index takes into account the available time on the machine before allocation, necessary time requirement of machine & available time on machine after allocation. This represented by
MTI [Oom p] = (tropm - ETmp ) / (taopm - ETmp ) (2)
here MTI [Oom ] represents the machining time index of the machine "m" after the allocation of operation "o" of part type "p" on machine "m" as per the nth set of operation allocation.
- Tool Slot Index: equivalent to each of operation allocation of part type on machine, the tool slot index takes into account the available tool slots on machine before allocation, necessary tool slot requirement of machine & available tool slots on machine after allocation.
TSI [Oom p] = (Tropm - E S mp) / (Taopm - ESmp) (3)
here TSI [Oom p] represents the tool slot index of machine "m" after the allocation operation of "o" of part type "p" on machine "m" as per the nth set of operation allocation.
- Priority Index: Priority index of set of operation allocation might be expressed as the product of average of machining time index & tool slots index of machine. This is represented by PI (ASpq) and expressed as:
(4)

If, TSI [Oom ]} ≥ 0
= ∝ (Infinity), otherwise.
Table 3 summarizes the different situation, which might arise during the evaluation of PI for a set of operation allocation.
Table 3
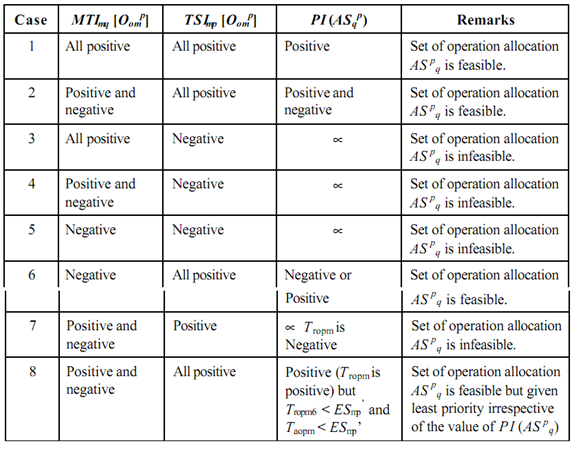
Decisions pertaining to set of operation allocation are to be made based on higher PI value. Some part types from the pool of part types remain unassigned due to violation of system constraints in the specified planning horizon. Accordingly to proposed methodology, part types are to be assigned on machines until various set of operation allocation observes tool slot constraints (until TSI [Oomp] is positive) as overloading of machines are allowed. After all of the part from the pool of part types have been assigned, the system unbalance mention the termination of the throughput is to be evaluated. Positive system unbalance mentions the termination of assignment process of the part types. If the system unbalance is -ve , then those part types are to be discovered whose rejection might bring system unbalance to minimum +ve value with minimum decreased in throughput. After discovering such types and its subsequent rejection, the status of machines (available time & available tool slot) are to be updated. Updation of machine status implies sum of corresponding machining time & tool slots on the respective machines on which the discarded part type's operations have allocated. If any part type has been discarded earlier on the ground of non-availability of tool slots (PI = ∝ for all A Sqp), then the similar is to be reallocated now and all other steps are repeated as practiced for unallocated part types.
Before any part types are to assign on machines, it is necessary to determine the sequence in which the specified part types are to be allocated on the machines. Mostly researchers have practiced standard sequencing rules such like LPT, SPT, MOPR, FIFO etc. for the determination part type's sequences. Among the above sequencing rules, "SPT" has been claimed to work better on an average. However, the determination of part type sequence using above rules, have been viewed by various researchers as the weakness of solution methodology for machine loading problem. Thus, in this research, attempts has been built to devise a part type sequencing criteria, which encompasses the various parameters such like batch size, overall processing time etc. to suit the objectives of difficulty. As per the recommended criteria of part type sequencing, contribution of every part type to these parameters is resolute. Parts types are to be arranged in sequence depend on the value of contribution (part types are arranged in descending order of contribution).
Contribution is to be evaluated based on the following expression:
α j = (W1 × β p1+W2 × β p2) / (W1 + W2) . . . ( 5)
where α p = Total contribution of the part types "p".
ßp1 = Contribution of the part type "p" to the batch size,
= (bp - [bp]min) / ([bp]max- [bp]min) . . . (6)
ßp2 = Contribution of the part type "p" to the total processing time,
= ([TPTp]max - TPTp) / ([TPTp]max - [TPT p]min) ........(7)
W1 = Weightage of batch size,
W2 = Weightage of total processing time,
TPT p = Total processing time of part type p
(8)
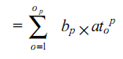
atop = Average unit processing time of operation "o" of the part type "p"
(9)
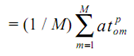
tcopm = Unit processing time of operation "o" of the part type "p" on machine "m".
W1 = W2 = 1(For our case),
0 < = ßp1 < = 1, 0 < = ßp2 < = 1, and 0 < = ap < = 1.