Continuous Casting
The traditional method of casting ingots is a batch procedure. Each of ingots is stripped from its mould after solidification & processed individually. In addition the defects like piping and micro-structural & chemical variations are present during the ingot. These problems are alleviated by continuous casting procedure, which generates better quality steels.
Continuous or strand casting was primary developed for casting non-ferrous metal strip. The procedure is now utilized for steel production, with major efficiency and productivity improvements and important cost reduction. A system for continuous casting is illustrated in Figure 6. The molten metal in the ladle is cleaned & nitrogen gas through this is blown for five to ten minutes to equlise the temperature. Then the metal is poured into a refractory-lines intermediate pouring vessel called as tundish where impurities are skimmed off. The tundish may hold as much as three tons of metal. The molten metal vessels through water-cooled copper mould and start to solidify as it travels downward along with a part supported by rollers.
Before beginning the casting procedure, a solid starter, or dummy, bar is inserted into the bottom of the mould. Then the molten metal is poured & freezes onto the dummy bar. The bar is withdrawn at the similar rate the metal is poured. The cooling rate is such that the metal develops a solidified skin to support itself throughout its travel downward at speed maintained at 25 mm/s. The shell thickness at exit end of the mould is approx 12 to 18 mm. Additional cooling is provided by water sprays along the travel path of the solidifying metal. Generally the moulds are coated with graphite or similar solid lubricants to decrease friction and adhesion at the mould walls. Vibration of moulds might further decrease friction and adhesion tendency.
The continuously cast metal might be cut into desired lengths by shearing or touch cutting, or it might be fed directly into a rolling mill for further desertion in thickness.Whether the steel is attained in form of ingots, stationary moulds or in a form of slab from constant casting procedure, it is converted into billets, blooms & slabs. The subsequent hot rolled products are explained as follows:
Blooms
Beams & angle sections, rails, bars of different sections.
Billets
Wire nails & wire mesh, pipes & tubes.
Slabs
Plates, strips & further cold rolled for decreasing thickness.
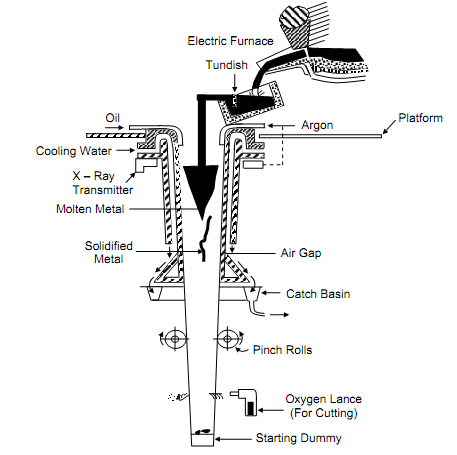
Figure: Continuous Casting Process of Steel Schematically