Combustion Efficiency
(a) Combustion efficiency is stated as the fraction of the chemical energy accessible in the fuel that is really released in the combustion procedure.
(b) Combustion efficiency is reduced by:
• Unfinished combustion caused by flame quenching, confirmed by the presence of substantial quantities of CO in the stack gas.
• Partly oxidized hydrocarbons or particles of unburned carbon exit as soot in the stack gas, or entrained in the ash from a coal-fired furnace.
(c) Combustion losses might be decreased by:
• Operating the furnace with surplus air.
• Providing enough time in the combustion region to give ample chance for all the carbon to respond with oxygen; the hydrogen in hydrocarbon fuels is oxidized quickly.
Combustion efficiency is optimized whenever the appropriate mixture of fuel and air is supplied therefore as to minimize the energy losses related with excess fuel and excess air.
Figure below illustrates the bell-shaped combustion efficiency curve for usual industrial fuel-burning equipment. It is significant to note that the rate of energy loss is six times greater on the surplus fuel side of the curve than it is on the surplus air side of the curve. As an outcome, most of the combustion control strategies approach optimum operation from the surplus air side of the curve therefore:
• To optimize effectiveness; and also
• To avoid dangerous excess fuel situations.
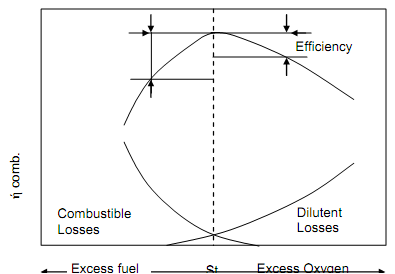
Figure: Effects of surplus Fuel and surplus Air on Combustion Efficiency
It might also be seen that nearer the FAR is to the optimum value, the less potential there is for fuel saving, and the larger the risk of harsh energy losses that take place on the excess fuel side of the curve. At higher surplus air levels, for every one per cent decrease in excess oxygen, a one per cent enhancement in combustion efficiency can be attained, at lower excess oxygen levels (3%), for every one per cent decrease excess oxygen, around 0.5% enhancement in combustion efficiency can be attained.