Quality Maintenance
Objectives
- To make quality through equipment,
- To ensure that no product defects are caused by faulty equipment, and
- To build a reliable production line (zero failures).
Methodology
To achieve these objectives TPM uses, MTBF and MQM (Man-Quality-Machine) management and also dissects operating mistakes to determine, if additional training or use of fail-safe devices.
Work Place Organisation and 5S Frame Work TPM organisation of work place along five dimensions is known as 5S (in Japanese) frame work
- Organisation
- Orderliness
- Attention to details
- Cleanliness
- Discipline
The focal idea of 5S work place organisation is identifying all the subtle abnormalities that might cause failures or defects if not discovered and treated.
Practicing 5S on regular basis encourages the formation of an improvement cycle beginning with reducing variations caused by abnormalities and then by creating stability and uniformity in manufacturing process and finally enhancing process analysis, which in turn leads to further improvements. These are discussed in detail at the end of this unit.
The purpose of TPM licensing system is to expand an operator's capabilities by developing new skills and promoting operational stability. The system also encourages acquisition of skills necessary to perform multiple jobs, creating a multi functional work force.
The usual management of Plan-Do-Check-Act cycle of work place organisation is shown in Figure.
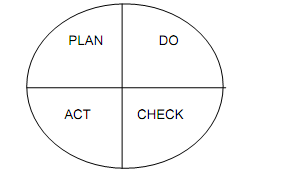
Figure: Quality Maintenance Management through PDCA
- Licensing program
- Procedures and Standards
- Training
- Layouts organised by type and function
- Inspection Plan
- Re-layouts
- Inspections and Hourly checks
- Evaluation
- Major clean up & cleaning work tools.