Factors That Affect Fracture
Many of such factors were considered when fatigue behaviour was discussed. One important service factor that affects fracture in service is the temperature and one of its effects is creep of metals .This has been explained earlier that a notch produces triaxial state of stress which tends to increase yield strength. Strain rate also helps increase yield strength while yield strength reduces if temperature increases. It may be worthwhile to note that both f.c.c. and b.c.c. metals tend to become brittle with decreasing temperature, i.e. their yield strength increases as temperature reduces. There is no ductile- to-brittle transition in f.c.c. metals and the reduction of ductility is continuous. While temperature reduces from ambient to liquid nitrogen the yield strength increases to twice its room temperature value. During the similar change of temperature the b.c.c. metals show ductile-to-brittle transition and yield strength at 196oC is about 3 to 8 times that of room temperature value. Ductility transition is found to occur in tension loading as in case of impact. This transition occurs when conditions are suitable for growth of microcracks into propagating fractures.
The existence of a transition temperature is because the resistances to shear and cleavage behave differently with temperature. The ductility will depend upon relative values of these two resistances. Flow stress is reached before the fracture stress above transition temperature but below the transition temperature the fracture stress is reached first. Figure shows the dependence of yield stress σy on temperature in simple tension test. A notched specimen has plastic constraints and hence shows higher yield strength, as can be seen in Figure. The fracture strength or cleavage strength σf, least affected by temperature is shown as fairly constant with increasing temperature. The transition temperature occurs at the intersection of flow and yield curves and note that in the presence of notch it occurs at a higher temperature, which could be much closer to room temperature. The recent studies have shown that at higher strain rates the ductility transition shifts towards room temperature faster than in case of notch.
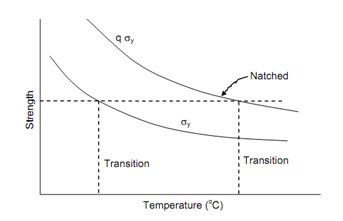
Figure: Temperature Dependence (Schematic)
The other reason for brittle fracture is increasing application in chemical or corrosive environment. Many high strength steels are susceptible to hydrogen embrittlement and fail over a period of time that varies with the applied stress and amount of hydrogen dissolved in steel. Fracture in oil well casings have been reported after periods of time ranging from days to months. Such fractures are hydrogen embrittled because of dissociation of H2S gas. Such fractures gave no warning of impending failure. Cadmium plated steel landing gears of jet aircrafts also failed due to hydrogen embrittlement.
Stress corrosion cracking is a phenomenon of brittle fracture of part subjected to stress in a hostile environment. The stress may be static, the failure is without warning and a few combinations of metal and environment have been identified for which no lower stress limit exists for avoiding stress corrosion brittle fracture. Such fractures occur at stress levels much below the yield strength. Copper alloys in ammonia atmosphere lose ductility and can fail in such short time as 100 to 200 hours.
Nuclear power poses problem of embrittlement due to exposure to fast neutron. Reactor pressure vessel made in steel is particularly subjected to such fracture incidence.
To conclude we make a list of factors that promote brittle fracture. Some of these were considered earlier.
1. Fatigue,
2. High strain rate,
3. Stress concentration (Triaxiality),
4. Low temperature,
5. Corrosion, and
6. Neutron exposure.