Hot Chamber Process:
In this procedure, a gooseneck is utilized for pumping the liquid metal into the die cavity. The gooseneck is submerged into the holding up furnace having the molten metal. The gooseneck is built of alloy, grey or ductile iron or of cast steel. A plunger built of alloy cast iron, that is hydraulically operated moves up in the gooseneck to uncover the entry port meant for the entry of liquid metal into the gooseneck. The plunger might then build up the necessary pressure for forcing the metal into the die cavity. A nozzle at the ending of the gooseneck is kept in close contact along the sprue situated in the cover die .
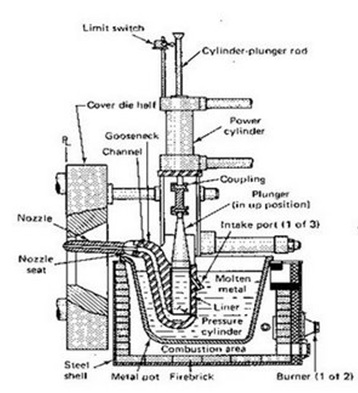
Figure : Hot Chamber Process
The cycle begins with the closing of the die while the plunger is in the uppermost position in the gooseneck, therefore facilitating the filling up of the gooseneck by the liquid metal. The plunger then begins moving down to force the metal in the gooseneck to be injected into the die cavity. The metal is after that held at the similar pressure until it is solidified. The die is opened up, and any cores if present, are also retracted. The plunger then moves back returning the unused liquid metal to the gooseneck. The casting that is in the ejector die is ejected now and at the similar time the plunger uncovers the filling hole, considering the liquid metal through the furnace to enter the gooseneck.
Air pressure needed for injecting the metal into the die is that of the order of 30-45 kg/cm2. Based upon its size, this hot chamber die casting machine might produce approximate 60 or more castings upto 20 kg each per hour and various hundred castings per hour for single impression castings weighing a few grams.