Cold Chamber Process:
The hot chamber procedure is utilized for most of the low melting temperature alloys such like lead, zinc and tin. For materials such like brass and aluminum, their high melting temperatures built it complex to cast them by hot chamber procedure, because gooseneck of the hot chamber machine is constantly in contact along the molten metal. Also liquid aluminum shall attack the gooseneck material and therefore hot chamber process is not utilized with aluminum alloys. In the cold chamber procedure, the molten metal is poured along a ladle into the hot chamber for each shot. This procedure reduces the contact time among the liquid metal and the hot chamber.
The operation begins along the spraying of die lubricants during the die cavity and closing the die while molten metal is ladled into the hot chamber of the machine either manually or through an auto ladles. An auto ladle is a form of robotic device, that automatically scoops molten aluminum from the holding furnace and pours it into the die at the exact example when needed in the casting cycle. The pouring temperature might be precisely controlled along the help of auto ladle and therefore the wished casting quality may be had. After that the plunger forces the metal in the die cavity and maintains the pressure until it solidifies. In the following step, the die opens up. The casting is ejected. At the similar time, plunger returns to its location completing the operation.
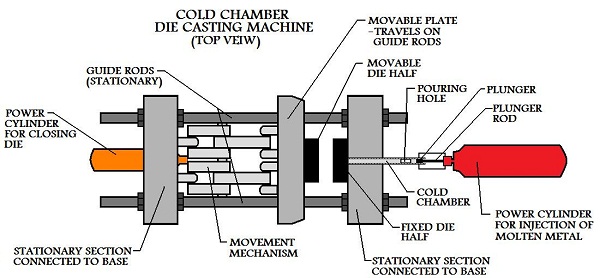