Significance of Condition Based Maintenance
Consider the following case:
In an office, there were three friends working namely, Qutub, Robert and Sairam. They have three different tastes and strategies in their life. For example, the health care strategy of these friends is interestingly in three different ways. Mr. Qutub does not care about his health and he will not take any precautionary measures at all for keeping up of good health. Further he eats any roadside eatables also. And he goes to doctor if and only if it is so necessary even when he is ill. But unfortunate thing is that most of the times, it becomes compulsory for him to spend on his ailments those become chronic due to mere negligence and ignorance. Unlike Mr. Qutub, Mr. Robert is so careful about his health. He never takes outside food and water if he feels it is not hygienic. He follows all the precautionary measures for his health and exercises jogging, swimming, yoga, etc. He goes to his family doctor in regular intervals and gets his blood pressure, blood sugar, etc. checked. Mr. Sairam found that Qutub is taking leave quite often on health reasons, sometimes even weeks together. Interestingly, he found that Robert is also taking leave for his health check up frequently though not really required. He noticed that Robert is much worried about his health and spending lot of money unnecessarily and his regular work is disturbed by himself. Therefore, he found another good policy that neither too much care like Robert nor careless like Qutub, he wanted to care his health in such a fashion that he visits his doctor when he just finds some symptoms of the ailment and thus prevents the illness. This strategy has saved most of leaves and money. It also gave a way for him to work without any tensions.
The above exemplary case clearly presents the significance of condition monitoring. If you imagine Qutub, Robert and Sairam as three machines, the strategy adopted on Qutub is operate to failure and corrective maintenance or breakdown maintenance while preventive maintenance is followed on Robert. The third kind is condition based maintenance followed on Sairam in which the down time and unnecessary costs can be controlled most effectively. In other words the first strategy is a failure based maintenance strategy, the second one is time-based maintenance and the third is condition based.
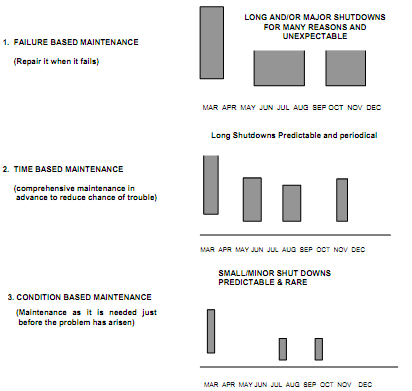
Figure: The Result of Maintenance Philosophies in a Typical Industry
The upper diagram in Figure shows what could happen to a typical plant if the method of operation of machine is to run until they fail and then repair them in order to restore the acceptable condition. This policy can prove to be expensive in the form of maintenance cost, lost productive hours and hazards to the personnel. Therefore, it is now well recognized especially in the case of large and expensive plant in order to avoid unscheduled shutdown, that it is much more economical to carryout Preventive Maintenance (PM) so that major breakdowns are avoided as shown in the middle diagram. The problem in preventive maintenance lies in the choice of an appropriate maintenance interval for the machine, because the actual running time before maintenance is really needed is not constant, but varies from one occasion to another and from one machine to another due to the difference in the operation of the machine and in the behaviour of its components and many more factors as discussed in this unit. If safe overall interval is chosen as shown in Figure there will be occasions when the machinery will be overhauled long before it is really necessary, while it could have run on for much longer without failing. This situation wastes production output and increases the incidence of human errors on reassemble of the machine. Too long an interval results in an unacceptable number of machine failures during operations. A compromise between these two extremes can be established by experience but machine failures will continue to occur. Some machine failures are the result of sudden events in which the machine condition deteriorates in few minutes. The greater number of machine failures however are the apex of long slow deterioration during which the machine gets progressively worse over a period of months or even years.
Therefore, a more satisfactory strategy is to carryout preventive maintenance at irregular intervals and to determine these intervals by the actual condition of the machine. In this method of Condition Based Maintenance (also known as Dynamic Predictive Maintenance or Diagnostic Maintenance) the plant is maintained just after some problem has arisen, but much before the possible breakdown. The maintenance activity is directed towards not only detection and prevention but also curing the particular problem. Although Condition Based Maintenance (CBM) as shown in Figure is applicable to the random failure mode, the characteristic of many plant items, it also has an obvious application to age-related failure of high cost plant such as where the manufacturer runs a number of old machines and equipment and he needs to be aware of the advent of deteriorating working conditions.