Static Tests
Tension Test
In this experiment we shall determine Young's modulus, the yield strength, fracture stress, critical strength, elongation and other properties of various tensile shafts or bars using Universal Testing Machine (UTM). After testing the graph is drawn from the data. For this we need various measurements of sample geometry to calculate engineering stress versus engineering strain to obtain the material properties. To construct the test, one end of standard specimen is attached to movable crosshead with other end fixed to a stationary member. The cross head is driven such that it stretches the specimen apart, i.e. the specimen is stretched under load until it beaks. Thus the tensile strength can be measured. The test is suitable to test the load capacity of shafts or bars trusses and some machine parts. However, such tests will be performed on specimen materials of the machine parts by
Original Equipment Manufacturer (OEM) of the equipment throughout or before manufacturing of the machine or throughout the design stage.
Hardness Tests
Hardness may be defined as the resistance of a material to deformation or indentation. Hardness is measured in Hardness Number and has no units. There are three methods in practice to measure Hardness Number. Thus we can classify the hardness tests in the following three ways :
- Brinell's Hardness Test
- Rockwell Hardness Test
- Vicker's Hardness Test
A brief description of these tests is given below:
Brinell's Hardness Test
In the Brinell hardness test a hardened steel ball of diameter 10 mm is forced into the surface, and an optical measuring device is used to measure the diameter of resulting indentation, d. Then the Brinell Hardness Number (BHN) can be calculated by the relation,
BHN = Load applied/ Surface area of indentation
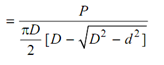
Where P = load applied, kg
= 3000 kg for steel
= 1000 kg for copper
= 500 kg for aluminium
D = diameter of steel ball, mm
d = diameter of indentation, mm
Rockwell Hardness Test
Rockwell Hardness Tests use different loads and penetrators (indenters), and depth of indentation is calibrated on a dial to a hardness number. We have two scales here, viz. B-Scale and C-Scale. Hardened steel ball with 100 kg total load is used for B-scale; while diamond cone (brale) with 150 kg total load is used for C-scale.
Rockwell Hardness Number on B-scale,
Diagnostic Maintenance
RB = 130 - (d /0.02)
and on C-scale,
RC = 100 - (d /0.02)
where d = depth of indentation
Vicker's Hardness Test
Vickers hardness test uses a surface based Diamond Pyramid with 136o apex angle between facets. It is forced into the surface with a suitable load ranging from 5 to 120 kg in steps of 5 kg. The test can be used for material with extreme hardness and case hardened parts. The Vickers Hardness Number (VHN) or Diamond Pyramid Hardness (DPH) is defined as the load (P) per unit area of the impression and is given by the equation.
DPH = 2P sin (α/2) / d2
where P = load applied on the diamond, kgf
d = diamond of the impression, mm
∝ = angle between the opposite faces of the diamond (136o)
Creep Test
The progressive deformation of material at constant stress is called creep. To determine the creep behaviour of the material, a constant load is applied to a specimen maintained at a constant temperature, and the strain (extension of specimen) is determined as a fraction of time. The creep test data is presented in the form of creep curve. The slope of the curve (d ε/d t) is referred to as the creep rate.