Effect of pH on the Relative Attack Rate of Iron in Water:
The hydrogen generally dissolved within reactor coolant does not have any detectable direct effect upon a corrosion rate of the iron and steels exposed to reactor coolant. It does, therefore, have a significant indirect effect through avoiding the accumulation of dissolved oxygen within reactor coolant that would accelerate corrosion. Dissolved oxygen reacts along with the protective hydrogen gas layer at a cathode to form water.
The condition and composition of the metal surfaces affects the corrosion rate. Irregular or deposits scale surfaces create areas on the metal whereas local corrosion could initiate and proceed at a faster rate than general. Certain alloys of metals have higher corrosion resistance than others.
While iron or steel is exposed to high temperature water, the rate of corrosion of the metal is experiential to decrease along with exposure time by during the early period of exposure. After a few thousand hours, a corrosion rate becomes associatively constant at a low value. During the previous period of exposure, when the corrosion rate is decreasing, an oxide film on the surface of the metal grows in thickness. Therefore, a rate at that the film grows decreases along with time. The thickness of the oxide film soon reaches a relatively constant value, and thereafter film thickness does not modify appreciably with further exposure. As might be expected then an associative constant corrosion rate and oxide film thickness is attained at about the same time. Since a strongly adhering corrosion film inhibits additional corrosion, great care is taken during the initial fill of reactor plants to promote formation of the best possible corrosion film. This procedure, referred to as pretreatment, or pickling, includes careful control of reactor coolant water chemistry and temperature in during the pretreatment period.
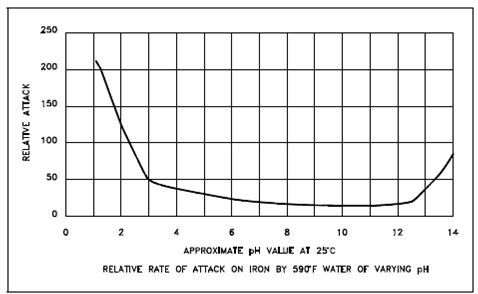
Figure: Effect of pH on the Relative Attack Rate of Iron in Water