PC Studies about the Process
PC studies provide the answers to these questions as:
(1) Does the process have the capability to meet specifications?
To answer this question, a process capability index, Cp, is frequently computed, where
C p = Tolerance Spread /6 σ = USL - LSL/6 σ
A value of Cp > 1.33 is considered good.
(2) Is the process well centered with respect to the desired nominal specification?
To answer of this question, the degree of bias (β) is computed, where
β = Estimated Process Mean - Nominal / ½ (Tolerance Spread)
= X ′ - Nominal / ½ (USL - LSL)
The condition for not producing rejects is

Or Cp (1 - β) > 1
Another capability index that combines both factors is
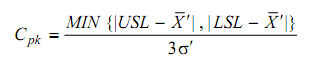
In response to the first question, the width of the histogram is compared with the specifications. In addition, the natural specification limits are computed and are then compared with the upper and lower tolerance limits. Three situations exist.
A. 6σ′ < USL - LSL or Cp > 1, or process variability is less than tolerance spread
B. 6σ′ = USL - LSL or Cp = 1, or process variability is equal to tolerance spread
C. 6σ′ > USL - LSL or Cp < 1, or process variability is greater than tolerance spread
In Situation I, the machine is able of meeting the tolerances applied by the designer. Generally, if process capability is on the order of two thirds to three quarters of the design tolerance, there is a high probability that the process shall produce all good parts over a long period of time. If the PC is on the order of one half or less of the design tolerance, it might be that the selected process is "too good'. That is, the company is making ball bearings whereas what is called for are marbles. In this case, it might be possible to trade off some precision in this procedure for looser specifications elsewhere, resulting in a total economic gain. Quality in well-behaved processes might be trained by checking the first & last part of a lot or production run. If these parts are good, after that the lot is certain to be good. It is called N = 2. Naturally if the lot size is 2 or less, this is 100% inspection. Sampling & control charts are also utilized under these conditions to maintain the process aim & variability.
Situation II must be treated like Situation III unless the process may be perfectly centered and maintained. Tool wear, that causes the distribution to shift, should be negligible. Then the situation might be treated as that in I, particularly if a small percentage of parts just outside tolerance is acceptable.