Design of Compound Compression Members:
You have observed that the load carrying capacity of compression members is greatly influenced by its slenderness ratio, a larger value of which reduces the allowable compressive stress. Since the effectual length is mostly fixed in such members, it is only the radius of gyration, which can be manipulated by the designer. In most of the rolled steel sections the minor radius of gyration is much smaller than the main one, therefore reducing the strength of the member. This can be overcome by arranging two or more sections such that the radii of gyration about the two principal axes are approximately the same. A number of such arrangements are shown in Figure.
Here two channels (Figures (a) and (b)) or two I-sections (Figure (c)) or four angle section (Figures (d), (e) and (f)) are joined together by suitable connecting system (shown by dotted lines in the figure). An exact spacing between the sections can be obtained by equating the moments of inertia Ixx = Iyy of the compound member. Therefore, an approximate value for the double channels is given in Figures (a) and (b).
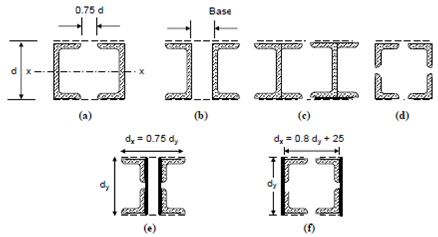
Figure
For the four angles joined with plates (Figure 10(e)) if dx ≈ 0.75 dy , then Iy will be not less than Ix. For the arrangement in Figure 10(f), keep dx ≈ 0.8 dy + 25 mm.
The major structural elements along with the connecting system must act as one element, without any joint failure, relative movement or distortion.
Since regards the lateral connecting system, shown through dotted lines in Figure, is concerned, two common methods used in structural engineering practice are (a) Lacing, and (b) Battened.