Feedback Elements
As mentioned earlier, the CNC machine tools generally are run with a closed loop control system. For this purpose it is necessary to provide appropriate feedback in order to achieve accurate control of the movement of the axes. The feedbacks that are in general utilized are the displacement and velocities of the individual axes in the machine tool. The typical positional sensors used in the CNC machine tools are following:
1. Encoders
2. Linear scales
The encoder is a transducer that is linked directly to the rotor or the lead screw and therefore does the simplest arrangement need no additional gearing. An optical rotary encoder changed the rotary motion of the motor into a sequence of digital pulses. The pulses counted to change to the position measurement. The optical encoder contains a disc having a number of accurately etched equidistant lines or slots along the periphery. The encoder disc is associated to the shaft of the machine whose rotary position has to be measured. The disc is placed between a light source (generally infra red LED) and a light measuring device (photo diode) as shown in Figure 6. When the disc rotates the lines are interrupted and the light measuring device counts the number of times the light is interrupted. By a careful counting and proper calculations it is possible to know the position traversed by the shaft.
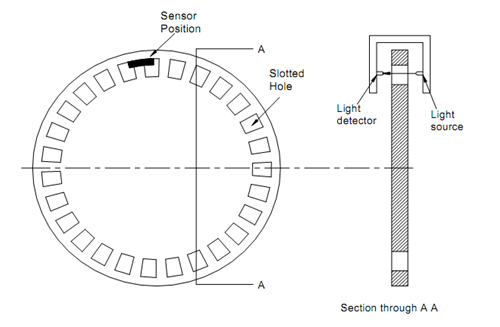
Figure 6: The Principle of Rotary Encoder with a Rotating Disc and Light Interruption for Position Measurement
The rotary encoder is normally mounted on the servo motor shaft or at the end of the lead screw as illustrated. This allows the control to calculate the actual distance moved from the rotary motion by using the lead of the lead screw. If the lead screw contains any backlash, then that will be reflected in the position indicated by the encoder. Therefore it becomes mandatory to remove the backlash in the lead screw to correctly get the position of the axis. Also it requires that the pitch of the lead screw be more correct over its entire length for exact sensing of the position.
To obviate such a predicament, it shall be better if the exact position attained by the slide might be measured through a transducer instead of the indirect way with the encoder. This might be done with the help of a linear scale associated directly to the slide. In this case the positional measurement will be direct and hence any of the inaccuracies present will not be affecting the measurement. The linear scale consists of a finely graduated grating made of either glass or stainless steel that is the measuring surface attached to one part of the slide. A scanning unit is fixed to other part. The scanning unit consists of a light source, a glass grid along graduated windows & some photo diodes as receptors. The basic principle employed in such measurements is that when two gratings overlap each other, a Moirè fringe pattern is formed corresponding to the displacement. The actual distance moved can be calculated by measuring the shift in the fringe pattern.