CNC Turning Centres
Similar to the milling machines the lathes are also provided with CNC controls. Majority of the components machined in the industry are having cylindrical shape and as such the CNC lathes are important machine tools. Alike to the machining centres, the CNC lathes are capable of carrying out a large range of operations, and therefore these are more appropriately called as turning centers. The main innovation provided in the CNC lathes is the provision of slant bed to help remove the chips from the machining zone more efficiently while allowing for a better and unobstructed view of the machining zone. A typical CNC turning centre is shown in Figure 18. Most of the turning centres are provided with a tool turret, generally which has a power of 8 to 12 tools of various types.
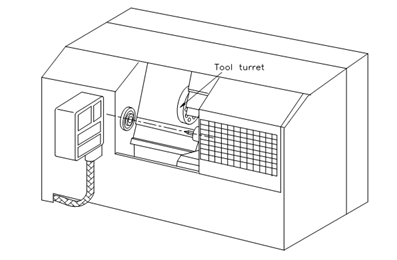
Figure 18: CNC Turning Centre with Slant Bed
One of the major developments that have taken place in the CNC turning centres is the development of turn-mill centre. If you go through some industrial components that are axi-symmetric in nature, you might notice that several of them cannot be completed in lathes alone. There shall be some operations for which the job may have to be taken to a milling machine, drilling machine or a grinder for finishing. Typical operations could be drilling of cross holes, milling of flats, slots, keyways etc. In such cases the completion of the job gets delayed which contributes to the additional cost as well as time. This can be taken care of generally by providing milling/grinding attachment on a lathe so that additional machine tools will not be required for completing the job.
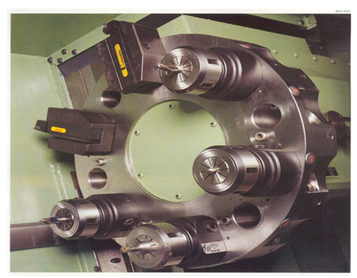
Figure 19: The Driven Tools in the Turret of a CNC Turn Mill Centre
For this to happen, it is necessary that the tools need to be provided with separate drive to provide the necessary motion to them. Throughout such operations, the spindle will not rotate and the tools get the necessary movements to position and move them as per the machining requirements. Such a machine tool is known as the CNC Turn Mill Centre. It can be seen in Fig 19 that the hole making tools in the turret such as twist drills, end mills, and boring bars are provided with rotary motion. Such tools are called driven tooling. Since the main spindle is not rotating during the machining operation with drilling and milling tools, it might be indexed suitably to obtain the necessary profiles. This is called the C-axis. The driven tooling can move in the X and Z directions like the normal turning centre. The combination of these 3-axes might make the machine tool really versatile and would allow for a range of complex surfaces to be produced. Typical jobs that can be machined by these machines is shown in Figure 20.
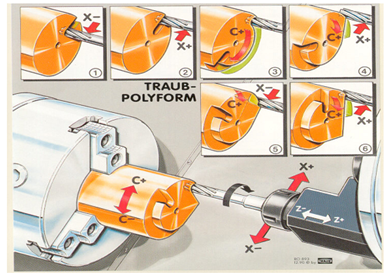
Figure 20: Typical Shapes of Component that can be Machined by the Combination of X, Z and C-Axis Movements