Abrasive Machining Processes
The abrasive machining processes are precision machining processes. They produce workpiece surfaces with a high degree of dimensional accuracy and surface smoothness.
Rough grinding, is sometimes used for removing excess material from the surfaces of castings, forgings, and similar workpiece which have not been machined. In rough grinding, a rotating abrasive grinding wheel is guided manually relative to a workpiece surface, which essentially differs from generally known grinding operation to obtain smooth finish and close tolerance in that grinding tool is machine held and guided. Abrasive are also used on belts or as powder paste.
Abrasives are hard materials with adequate toughness. A number of materials may serve as abrasive, but in the abrasive machining processes today the three commonly used abrasives are diamond (a form of pure carbon), silicon carbide (SiC), & aluminium oxide (Al2O3). Diamond is the hardest material in all known material, with a hardness of 10 on the Mohs’ scale. However, due to its relatively high cost, diamond is utilized only for those applications which require it use and justify its higher cost. Some of abrasives are found in the earth’s surface as natural abrasives, and diamond is one in which. Aluminium oxide with varying proportions of impurities is also found as a natural abrasive. However, in order to control purity and secure uniformity, practically all aluminium oxide and all silicon carbide used today in the abrasive machining processes are produced synthetically. In Table, showing relative hardness, it might be noted that silicon carbide is somewhat harder than aluminium oxide. Alternatively, aluminium oxide is tougher than silicon carbide, with the result that its grains shall not fracture as readily. Aluminium oxide is utilized for grinding steels, mallable iron and other materials with high tensile strength. Silicon carbide is employed for grinding cast iron, aluminium casting, bronze, and other materials along low tensile strength. Green SiC (99% SiC) is utilized to grind cemented carbide.
Table: Relative Hardnesses of Some Materials
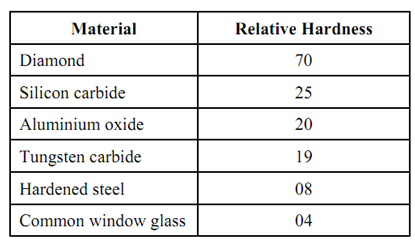
Abrasive material, whether produced synthetically or discovered in nature, is crushed to particles of desired size. These particles are called as “grains”, or grits. For some of application the crushing is continued till the abrasive becomes a fine powder, frequently called“flour”. As sands, abrasive grains are passed through a set of standard-mesh sieves to separate them according to grain size. Grain size is designated through the mesh of the finest standard sieve through which the grains shall pass. The size is explained by number of meshes per linear inch. The standard meshes are from 10 to 600. The size is known as grit size code. The code is explained below:
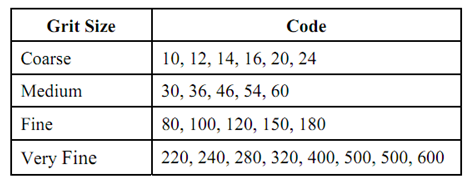
Coarse and medium size grits are utilized for soft material whereas fine and very fine size are utilized for hard materials. Abrasive flours, which are too fine for separating with sieves, must be segregated by a flotation method in a liquid. abrasive might be used as loose grins or flours as in polishing, lapping and buffing. For honing, grinding, and superfinishing, the abrasive grains are bonded together into shapes called as grinding wheels, sticks and stones. In any case, the abrasive grains that suitably held and moved across a workpiece surface, eliminate material by a cutting action. This cutting action generates minute chips and it is in fact similar to the cutting action of other cutting tools.
Grinding is accomplished along the use of an abrasive grinding wheel, mounted on a appropriate machine & rotated at a appropriate rotational velocity. In precision grinding, movements of the grinding wheels relative to the workpiece are accurately guided by the machine. Grinding is done on a Workpiece for three principal reasons.
1. To machine materials which are too hard for other machining methods which use cutting tools.
2. To produce surfaces within closer dimensional tolerances.
3. To produce surfaces with a higher degree of smoothness.
Some grinding processes are economical for the removal of relatively large amounts of material. For other grinding processes, power requirements, labour costs, and tools costs are higher than for other cutting processes. Materials harder than regarding Rockwell C45 might not be machined by the machining processes which use cutting tools. They must be machined by grinding, by some other abrasive machining procedure, or by a suitable newly developed process.
While a workpiece is to be hardened, the majority of the excess material should be removed by some other machining process prior to hardening. Only a minimum of excess material must be left on the workpiece surface to be eliminated by grinding after the hardening. This excess material is called as the “grinding allowance”. Grinding allowance shall have to be slightly larger for some workpieces, which might change shape slightly during heat treatment. A vital advantage of grinding is the small size of the cutting edges on the grains. As the cutting takes place in exceedingly small amount it might be controlled to hold close dimensional tolerances and to generate smooth surfaces. Workpiece of either hard or soft materials are frequently ground to take benefit of this capability of grinding. Dimensional tolerances as small as 0.0025 μ & surface smoothness’s of 0.025 μ are readily attained by grinding. Even these might be exceeded by utilizing better than average equipment, care and skill.